Ink jet printer
a jet printer and printer body technology, applied in the direction of printing, other printing apparatus, article separation, etc., can solve the problems of scratch resistance, negative effects of light scattering, glossiness of printed images, etc., and achieve the effect of improving image quality
- Summary
- Abstract
- Description
- Claims
- Application Information
AI Technical Summary
Benefits of technology
Problems solved by technology
Method used
Image
Examples
Embodiment Construction
[0020] As is shown in FIG. 1, a hot-melt ink jet printer comprises a platen 10 which is intermittently driven to rotate in order to advance a sheet 12, e. g. a sheet of paper, in a direction indicated by an arrow A over the top surface of a sheet support plate 14. A number of transport rollers 16 are rotatably supported in a cover plate 18 and form a transport nip with the platen 10, so that the sheet 12, which is supplied from a reel (not shown) via a guide plate 20, is paid out through a gap formed between an edge of the cover plate 18 and the surface of the sheet support plate 14.
[0021] A carriage 22 which includes a number of ink jet printheads (not shown) is mounted above the sheet support plate 14 so as to reciprocate in the direction of arrows B across the sheet 12. In each pass of the carriage 22, a number of pixel lines are printed on the sheet 12 by means of the printheads which eject droplets of hot melt ink onto the sheet in accordance with image information supplied to...
PUM
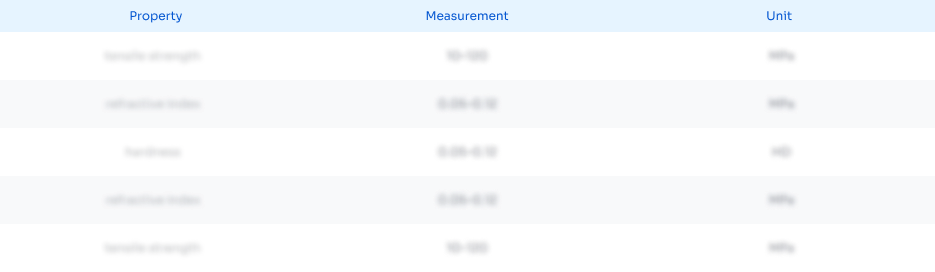
Abstract
Description
Claims
Application Information

- Generate Ideas
- Intellectual Property
- Life Sciences
- Materials
- Tech Scout
- Unparalleled Data Quality
- Higher Quality Content
- 60% Fewer Hallucinations
Browse by: Latest US Patents, China's latest patents, Technical Efficacy Thesaurus, Application Domain, Technology Topic, Popular Technical Reports.
© 2025 PatSnap. All rights reserved.Legal|Privacy policy|Modern Slavery Act Transparency Statement|Sitemap|About US| Contact US: help@patsnap.com