Drive unit for horizontally turning rotational solid
a technology of rotating solids and drive units, which is applied in the direction of manufacturing tools, grain treatment, and gearing, can solve the problem of large height of the required foundation for the gear train, and achieve the effect of less space and cost-effectiveness
- Summary
- Abstract
- Description
- Claims
- Application Information
AI Technical Summary
Benefits of technology
Problems solved by technology
Method used
Image
Examples
Embodiment Construction
[0016]FIG. 1 shows the gear train housing 1 of the drive unit for a cylindrical body of revolution 2 in end view relative to the axis of rotation 3 of the body of revolution 2. The body of revolution 2, for example, is the grinding drum of a cement mill, and for better clarity the outer contour of this body of revolution is shown only in dashed lines.
[0017] In the gear train housing 1 of the drive unit, the gears are arranged in the form of a speed-reducing gear train, with the two driven gears 4 and 4′ protruding in the direction of the axis of rotation 3 of the body of revolution 2. The teeth of the driven gears 4 and 4′ now engage with the gear rim 6 (only a portion of which is shown) arranged in this place on the periphery of the body of revolution 2. The engaging of the upper driving gear 4 occurs at an angle α of at least approximately 25° to 40° in relation to the horizontal transverse axis of the body of revolution 2. The lower pinion 4′ thus has an angle of engagement of a...
PUM
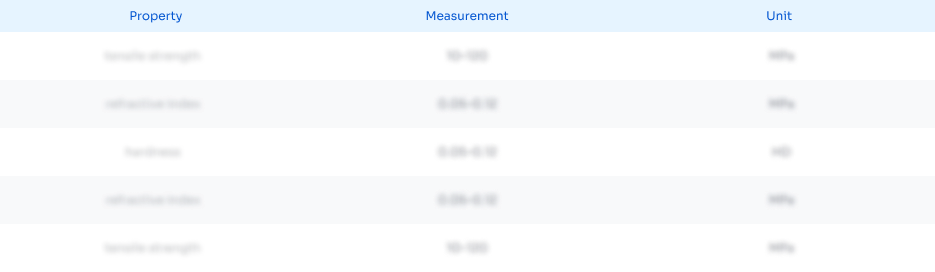
Abstract
Description
Claims
Application Information

- R&D
- Intellectual Property
- Life Sciences
- Materials
- Tech Scout
- Unparalleled Data Quality
- Higher Quality Content
- 60% Fewer Hallucinations
Browse by: Latest US Patents, China's latest patents, Technical Efficacy Thesaurus, Application Domain, Technology Topic, Popular Technical Reports.
© 2025 PatSnap. All rights reserved.Legal|Privacy policy|Modern Slavery Act Transparency Statement|Sitemap|About US| Contact US: help@patsnap.com