Papermaking press felt and papermaking press apparatus
- Summary
- Abstract
- Description
- Claims
- Application Information
AI Technical Summary
Benefits of technology
Problems solved by technology
Method used
Image
Examples
example 1
[0070] As shown in FIG. 2, a felt has been fabricated by layering the following woven fabric 220 as the base material B on the base material A (210) to constitute the base material 200, and further forming the staple fiber layer 300 (11 dtex, 600 g / m2)
Structure of the Woven Fabric 220:
[0071] (1) MD yarn: The twine specified below has been employed. [0072] (a) Twisting condition: “2 / 2 / 220”[0073] (b) Preliminary twisting: S-twist, 42 times per meter [0074] (c) Final twisting: Z-twist, 30 times per meter [0075] (d) Twisting ratio (preliminary / final): 1.40 [0076] (2) CD yarn: single yarn (fineness 330 dtex) [0077] (3) Weaving: [0078] MD yarn: 40 rows / 5 cm, CD yarn: 34 rows / 5 cm 3 / 1 plain endless single woven
example 2
[0079] A felt of a similar structure to that of the example 1 has been fabricated, except that the following woven fabric 230 has been employed as the base material B instead of the woven fabric 220. In other words, 230 is layered instead of 220 in FIG. 2.
Structure of the Woven Fabric 230:
[0080] (1) MD yarn, CD yarn: The same as those of example 1. [0081] (2) Weaving: [0082] MD yarn: 40 rows / 5 cm, CD yarn: 34 rows / 5 cm [0083] 3 / 1 plain single woven with an end closed, wound twice to constitute the layered woven fabric 230.
example 3
[0084] A felt of a similar structure to that of the example 2 has been fabricated, except that the woven fabric 240 in which the MD yarn and the CD yarn are replaced with each other has been employed as the base material B, instead of the woven fabric 230. In other words, 240 is layered instead of 220 in FIG. 2.
PUM
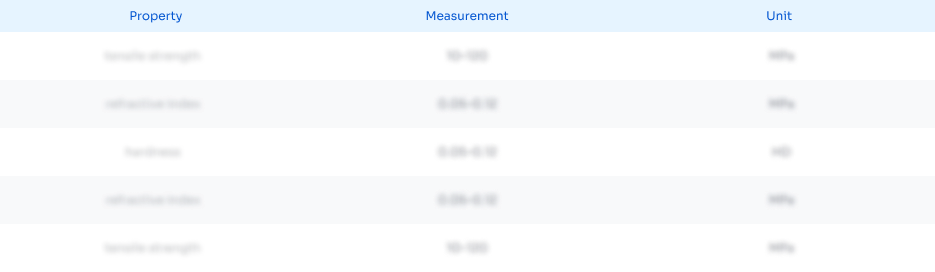
Abstract
Description
Claims
Application Information

- R&D
- Intellectual Property
- Life Sciences
- Materials
- Tech Scout
- Unparalleled Data Quality
- Higher Quality Content
- 60% Fewer Hallucinations
Browse by: Latest US Patents, China's latest patents, Technical Efficacy Thesaurus, Application Domain, Technology Topic, Popular Technical Reports.
© 2025 PatSnap. All rights reserved.Legal|Privacy policy|Modern Slavery Act Transparency Statement|Sitemap|About US| Contact US: help@patsnap.com