Frame structure for vehicle
a frame structure and vehicle technology, applied in the direction of roofs, vehicle arrangements, transportation and packaging, etc., can solve the problems of lateral buckling under a generally constant crushing reaction (force), the strength/rigidity of the floor member tends not to meet the impact deformation requirements, and the transfer of lateral buckling toward the section b owing to the formation of an abrupt change in lateral rigidity
- Summary
- Abstract
- Description
- Claims
- Application Information
AI Technical Summary
Problems solved by technology
Method used
Image
Examples
second embodiment
[0066] FIG. 11 shows the present invention. In this embodiment, the tunnel section 1A is also formed of a single wall, while the remaining parts 1B, 1C, 1D are respectively formed to have closed cross-sections composed of the upper and lower walls 21, 22, the partition ribs 23, 24, 25 and the reinforcement ribs 26 to 30. Further, the closed cross-sectional heights of sections B, C, D, are also such that h.sub.D>h.sub.C>h.sub.B.
[0067] In the above-mentioned basic structure, the physical characteristics of sections A to D of the second embodiment are quite similar to the first embodiment. However, in section C, the wall thickness t.sub.6 of the upper wall 21 in the section C is greater than the wall thickness t.sub.7 of the lower wall 22 in the same section due to the requirements of floor rigidity against the seat loads (t.sub.6
[0068] In the case of different wall thicknesses t of the inner and outer walls 21, 22 in section C, it is necessary that the inner and outer walls ...
third and fourth embodiments
[0070] FIGS. 12 and 13 show modifications of the high-strength part B.sub.1 while FIG. 14 shows the deformation produced by a side impact.
[0071] In FIG. 12, section B is formed so that the wall thickness t.sub.4A, t.sub.9A of the high-strength part B.sub.1 are larger than the wall thickness t.sub.4, t.sub.9 of the other parts except for the high strength part B.sub.1. Also in FIG. 13, section B is formed so that the wall thickness t.sub.4A, t.sub.9A, t.sub.9B of the high-strength part B.sub.1 is greater than the wall thickness t.sub.4, t.sub.9 of the other part which the exception of the high strength part B.sub.1. However, the average lateral rigidity of the section B including the high-strength part B.sub.1 is substantially similar to or less than that of the section C. As shown in FIG. 14, when the vehicle is subjected to side impact, the deformation is abruptly decreased upon reaching the outboard edge of the high-strength part / section B.sub.1.
[0072] As mentioned above, the floo...
PUM
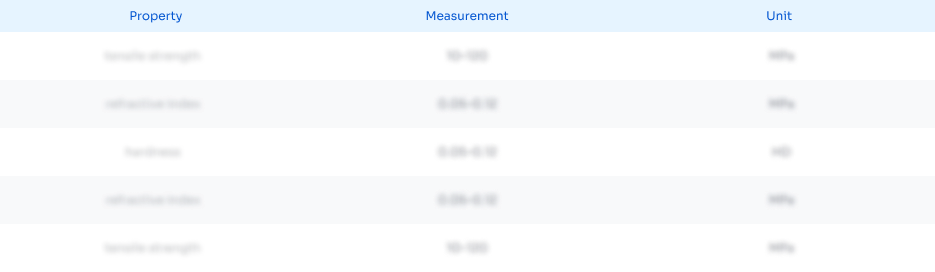
Abstract
Description
Claims
Application Information

- R&D
- Intellectual Property
- Life Sciences
- Materials
- Tech Scout
- Unparalleled Data Quality
- Higher Quality Content
- 60% Fewer Hallucinations
Browse by: Latest US Patents, China's latest patents, Technical Efficacy Thesaurus, Application Domain, Technology Topic, Popular Technical Reports.
© 2025 PatSnap. All rights reserved.Legal|Privacy policy|Modern Slavery Act Transparency Statement|Sitemap|About US| Contact US: help@patsnap.com