Automatic steam control system of defibrator
A technology of automatic control system and thermal mill, which is applied in the pipeline system, mechanical equipment, gas/liquid distribution and storage, etc., and can solve the problem that the temperature and pressure of saturated steam are relatively strict, manual control valves cannot meet production needs, and steam volume Oversize and other problems, to achieve reasonable steam supply, reduce energy consumption, and improve production efficiency
- Summary
- Abstract
- Description
- Claims
- Application Information
AI Technical Summary
Problems solved by technology
Method used
Image
Examples
Embodiment Construction
[0020] Below in conjunction with accompanying drawing 1,2,3 and embodiment, the present invention will be further described:
[0021] One embodiment of the present invention is the steam automatic control system of a heat refiner as shown in Figure 2 . The diameter of the grinding disc of the thermal grinding host 106 of this thermal grinding machine is 44 inches (diameter 1118 mm), the grinding disc rotating speed is 1490 rpm, and the power of the main motor is 2000 kilowatts.
[0022] This embodiment is composed of many pneumatic components shown in Figure 2, including steam pipes, pneumatic regulating valves, pneumatic ball valves, pressure transmitters, platinum thermal resistors, safety valves, stop valves and steam traps. The installation and connection steps of the system are as follows:
[0023] Saturated steam enters the pipeline system from the steam main pipe 301 and is divided into pipelines 302 and 303 through the tee pipe. The pipeline 302 mainly enters the pre...
PUM
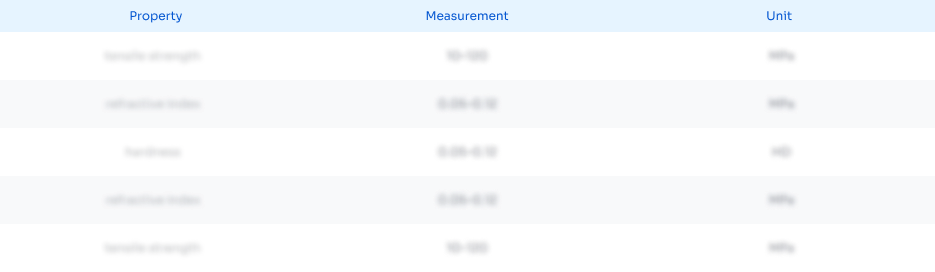
Abstract
Description
Claims
Application Information

- R&D
- Intellectual Property
- Life Sciences
- Materials
- Tech Scout
- Unparalleled Data Quality
- Higher Quality Content
- 60% Fewer Hallucinations
Browse by: Latest US Patents, China's latest patents, Technical Efficacy Thesaurus, Application Domain, Technology Topic, Popular Technical Reports.
© 2025 PatSnap. All rights reserved.Legal|Privacy policy|Modern Slavery Act Transparency Statement|Sitemap|About US| Contact US: help@patsnap.com