Method for producing modified rosin ester resin composition for lithographic ink varnish and method for producing lithographic ink varnish
A technology of resin composition and lithographic ink, applied in the direction of ink, natural resin chemical modification, application, etc., can solve the problems of difficulty in obtaining sufficient viscoelasticity of lithographic ink, difficult reaction, pollution and flying ink, etc., and achieve the suppression of printing incompatibility , high resin solubility, effective effect of environmental improvement
- Summary
- Abstract
- Description
- Claims
- Application Information
AI Technical Summary
Problems solved by technology
Method used
Examples
Embodiment 1
[0044] Add 1000 g of rosin (acid value 165KOHmg / g) and 106 g of fumaric acid to the reaction vessel, and heat and stir at 220° C. for 1 hour under nitrogen flow to obtain an acid value of 242 KOHmg / g containing acid-modified rosin and unreacted rosin After adding and mixing 317 g of linseed oil and 162 g of pentaerythritol, 1.5 g of magnesium oxide as a catalyst was added, stirred and mixed, and the temperature in the reaction vessel reached 161°C. Then, the reaction container was heated, and the temperature was raised to 270°C at a temperature increase rate of 30°C / hour for reaction, and then reacted at 270°C so that the acid value became 20KOHmg / g or less to obtain modified rosin ester resin and unreacted flax Modified rosin ester resin composition (R-1) for lithographic ink varnish of the present invention comprising kernel oil and pentaerythritol. About the obtained modified rosin ester resin composition (R-1) for lithographic ink varnishes, the acid value, weight average ...
Embodiment 2
[0051] Add 1000g of rosin (acid value 165KOHmg / g) and 106g of fumaric acid to the reaction vessel, and heat and stir at 200°C for 30 minutes under nitrogen flow to obtain an acid value of 240KOHmg / g containing acid-modified rosin and unreacted rosin After adding and mixing 240 g of linseed oil and 162 g of pentaerythritol, 1.5 g of magnesium oxide as a catalyst was added, stirred and mixed, and the temperature in the reaction vessel reached 155°C. Then, the reaction vessel was heated, and the temperature was raised to 260° C. while reacting at a heating rate of 30° C. / hour, and then reacted at 260° C. to make the acid value below 25 KOHmg / g to obtain modified rosin ester resin and unreacted Modified rosin ester resin composition (R-2) for lithographic ink varnish of the present invention comprising linseed oil and pentaerythritol. The acid value, weight average molecular weight, viscosity, and solvent solubility (AF Solvent No. 7 solubility) of the obtained modified rosin este...
Embodiment 3
[0053] Add 1000g of rosin (acid value 165KOHmg / g) and 106g of fumaric acid to the reaction vessel, and heat and stir at 200°C for 30 minutes under nitrogen flow to obtain an acid value of 240KOHmg / g containing acid-modified rosin and unreacted rosin After adding and mixing 160 g of linseed oil and 162 g of pentaerythritol, 1.5 g of magnesium oxide as a catalyst was added and stirred and mixed, and the temperature in the reaction vessel reached 160°C. , then, heat the reaction vessel, and then react at 260°C with a heating rate of 30°C / hour to 260°C, and then react at 260°C to make the acid value below 30KOHmg / g to obtain modified rosin ester resin and unreacted Linseed oil and pentaerythritol modified rosin ester resin composition (R-3) for lithographic ink varnish of the present invention. The acid value, weight average molecular weight, viscosity, and solvent solubility (AF Solvent No. 7 solubility) of the obtained modified rosin ester resin composition for lithographic ink ...
PUM
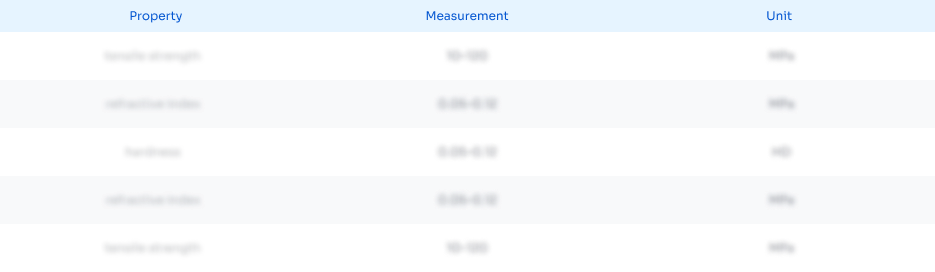
Abstract
Description
Claims
Application Information

- R&D
- Intellectual Property
- Life Sciences
- Materials
- Tech Scout
- Unparalleled Data Quality
- Higher Quality Content
- 60% Fewer Hallucinations
Browse by: Latest US Patents, China's latest patents, Technical Efficacy Thesaurus, Application Domain, Technology Topic, Popular Technical Reports.
© 2025 PatSnap. All rights reserved.Legal|Privacy policy|Modern Slavery Act Transparency Statement|Sitemap|About US| Contact US: help@patsnap.com