Concrete additive for inhibiting alkali aggregate reaction and its production
A concrete admixture and preparation process technology, applied in the application, ceramic products, other household appliances, etc., can solve the problems of unfavorable early strength of concrete, pollute the environment, etc., and achieve the effect of inhibiting the reaction of alkali silicic acid
- Summary
- Abstract
- Description
- Claims
- Application Information
AI Technical Summary
Problems solved by technology
Method used
Examples
Embodiment 1
[0013] Immerse natural zeolite powder in 1mol / L (NH 4 ) 2 CO 3 In aqueous solution, boil for 1 hour to obtain ammonium zeolite, then dry at 400°C for 2 hours to remove NH 3 and activate H + Adsorption site, to obtain concrete admixture, when replacing 5% of cement in equivalent amount, according to the standard of American Society for Testing and Materials (ASTM C441 standard), the 14-day expansion rate of glass mortar rods is 0.0883%, which is 69.5% lower than that of reference specimens.
Embodiment 2
[0015] Immerse natural zeolite powder in 1mol / L (NH 4 ) 2 CO 3 Boiling 1h in the aqueous solution, other measures are with embodiment 1, made concrete admixture, according to American Society for Testing and Materials standard (ASTM C441 standard) during the time of dosage 5%, detect glass mortar bar 14 days expansion rate is 0.0812%, relatively The baseline test piece was reduced by 72%.
Embodiment 3
[0017] Immerse natural zeolite powder in 1mol / L (NH 4 ) 2 CO 3 Boiling 1h in the aqueous solution, other measures are with embodiment 1, made concrete admixture, according to American Society for Testing and Materials standard (ASTM C441 standard) during the time of dosage 5%, detect glass mortar bar 14 days expansion rate is 0.0812%, relatively The baseline test piece was reduced by 72%.
PUM
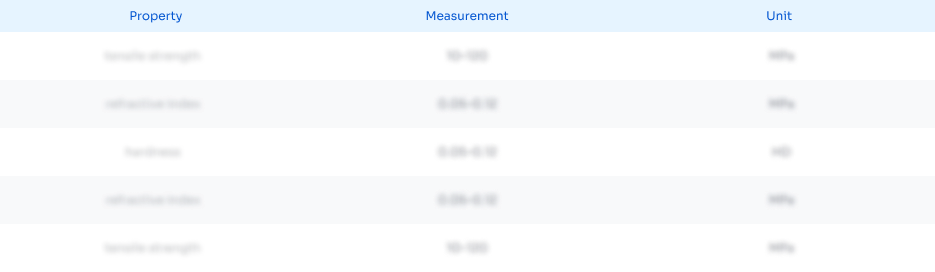
Abstract
Description
Claims
Application Information

- R&D
- Intellectual Property
- Life Sciences
- Materials
- Tech Scout
- Unparalleled Data Quality
- Higher Quality Content
- 60% Fewer Hallucinations
Browse by: Latest US Patents, China's latest patents, Technical Efficacy Thesaurus, Application Domain, Technology Topic, Popular Technical Reports.
© 2025 PatSnap. All rights reserved.Legal|Privacy policy|Modern Slavery Act Transparency Statement|Sitemap|About US| Contact US: help@patsnap.com