Collaborative work of multiple lidars, and dat processing method
A lidar, collaborative work technology, applied in the re-radiation of electromagnetic waves, the use of re-radiation, measurement devices, etc., can solve the problems of poor reliability of error redundancy, insufficient system response speed, etc., to ensure production, improve scanning accuracy, strong The effect of system redundancy and fault tolerance
- Summary
- Abstract
- Description
- Claims
- Application Information
AI Technical Summary
Problems solved by technology
Method used
Image
Examples
Embodiment Construction
[0055] The technology of the present invention is realized by a multi-laser radar system, and the specific workflow is as follows:
[0056] 1. In the on-site installation stage of the system, the weight distribution network is trained according to the on-site measured data, and the initial weight table based on distance and reflectivity is established;
[0057] 2. When the MLRS starts, it performs a state self-check, performs a series of initializations, divides the scanning area of the target, and determines the scanning area of each working radar;
[0058] 3. Each radar working sub-thread independently executes the scanning task, preprocesses the message to generate measurement data, and calculates the data weight by table look-up interpolation, and generates the confidence distance domain of the scanning data;
[0059] 4. During MLRS operation, the monitoring module performs automatic fault diagnosis and shielding in real time. Carry out validity verification based on ...
PUM
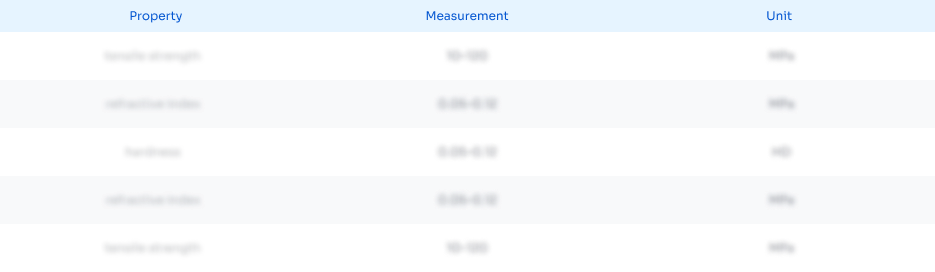
Abstract
Description
Claims
Application Information

- Generate Ideas
- Intellectual Property
- Life Sciences
- Materials
- Tech Scout
- Unparalleled Data Quality
- Higher Quality Content
- 60% Fewer Hallucinations
Browse by: Latest US Patents, China's latest patents, Technical Efficacy Thesaurus, Application Domain, Technology Topic, Popular Technical Reports.
© 2025 PatSnap. All rights reserved.Legal|Privacy policy|Modern Slavery Act Transparency Statement|Sitemap|About US| Contact US: help@patsnap.com