Motor controller
A control device and motor technology, applied in motor generator control, AC motor control, electronic commutation motor control, etc., can solve the deterioration of estimation accuracy, difficulty in improving magnetic pole position accuracy, friction fluctuation, stable disturbance load reliability reduction, etc. question
- Summary
- Abstract
- Description
- Claims
- Application Information
AI Technical Summary
Problems solved by technology
Method used
Image
Examples
Embodiment approach 1
[0042] figure 1 It is a figure which shows the structure of the motor control apparatus concerning Embodiment 1 of this invention. also, figure 2 It is a figure which shows an example of the structure of the shaft deviation detection part in the motor control apparatus concerning Embodiment 1 of this invention. In addition, FIG. 3 is a diagram illustrating the relationship between the dq axis (dm-qm axis) of the actual motor and the dq axis (dc-qc axis) of the control.
[0043] use figure 1 ˜ FIG. 3 , the processing operation of the motor control device according to Embodiment 1 will be described.
[0044] exist figure 1 , the speed control unit 1 inputs the speed command wm * and the actual speed wm, follow the speed command wm with the actual speed wm * The way, using PI control, etc., for speed control, output q-axis current command iqc * . In addition, the current control unit 2 inputs the d-axis current command idc * , q-axis current command iqc * , d-axis curr...
Embodiment approach 2
[0078] Next, use Figure 4 Next, the processing operation of the shaft deviation detection unit 11b in the motor control device according to the second embodiment will be described. exist Figure 4 Among them, 101, 102, 104, 105 and figure 2 The same, and its description is omitted. Figure 4 The structure of the axis misalignment detection unit 11b shown is that in figure 2 Between the input filters 101, 102 and the adaptive input calculation unit 103a in the axis deviation detecting unit 11a shown, a sign detector 106 as a first sign detector and a sign detector 107 as a second sign detector are inserted. .
[0079] The d-axis signal idh for axis deviation detection and the q-axis signal iqh for axis deviation detection after filter processing by the input filters 101 and 102 are input, and the signs are detected by the sign detectors 106 and 107 as signed axis deviation detection d The axis signal sign(idh) and the signed q-axis signal sign(iqh) for axis deviation de...
Embodiment approach 3
[0085] Next, use Figure 5 The processing operation of the shaft deviation detection unit 11c in the motor control device according to Embodiment 3 will be described.
[0086] Using the input filters 101 and 102, the d-axis current command idc of the input shaft deviation detection unit 11c * and q-axis current command iqc * (or torque current error iqm) is filtered, and the d-axis signal idh for shaft deviation detection and the q-axis signal iqh for shaft deviation detection are output.
[0087] The estimated output computing unit 108 multiplies the shaft deviation detection d-axis signal idh filtered by the input filter 101 by an output shaft deflection estimated value Δθ^ to be described later, and outputs an estimated output (idh×Δθ^). In addition, the axis deviation error calculation unit 109 acquires the difference between the axis deviation detection q-axis signal iqh filtered by the input filter 102 and the estimated output (idh×Δθ^) output from the estimated output...
PUM
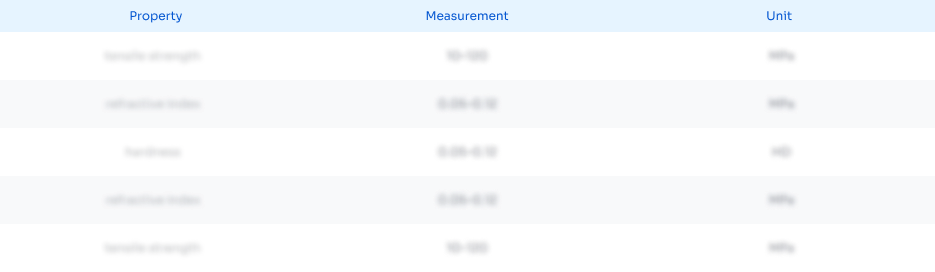
Abstract
Description
Claims
Application Information

- Generate Ideas
- Intellectual Property
- Life Sciences
- Materials
- Tech Scout
- Unparalleled Data Quality
- Higher Quality Content
- 60% Fewer Hallucinations
Browse by: Latest US Patents, China's latest patents, Technical Efficacy Thesaurus, Application Domain, Technology Topic, Popular Technical Reports.
© 2025 PatSnap. All rights reserved.Legal|Privacy policy|Modern Slavery Act Transparency Statement|Sitemap|About US| Contact US: help@patsnap.com