Centrifugal extruder
An extruder and centrifugal technology, which is applied in the field of screw extruders, can solve the problems of energy waste and large friction loss, and achieve the effects of reducing energy consumption, reducing friction energy consumption, and improving heating efficiency
- Summary
- Abstract
- Description
- Claims
- Application Information
AI Technical Summary
Problems solved by technology
Method used
Image
Examples
Embodiment 1
[0012] Taking the extrusion of high-density polyethylene pellets as an example, the equipment structure is as follows figure 1 As shown, the maximum diameter at the outlet of the centrifugal feeding drum 3 is Φ200mm, the inner cone angle of the drum 3 is 70°, and the cone angle of the inner core 5 is 45°. The outlet of the feeding sleeve 6 is a 70×30 rectangular hole, the rotating speed of the centrifugal feeding drum 3 is 1800 rpm, the heating temperature of the centrifugal feeding drum 3 and the feeding sleeve 6 is 100-160°C, the heating of the barrel 10 The temperature is 180-190°C, the diameter of the screw is Φ45, and the aspect ratio is 17. The screw grooves on the front 7D length of the screw are equidistant and gradual grooves, and the rear 10D lengths are equidistant and equal depth grooves. The screw speed is 10-100 rpm, and the driving power of the motor-reducer 9 is 1 / 2 of the driving power of the common ф45 extruder motor. However, the driving power of the motor ...
PUM
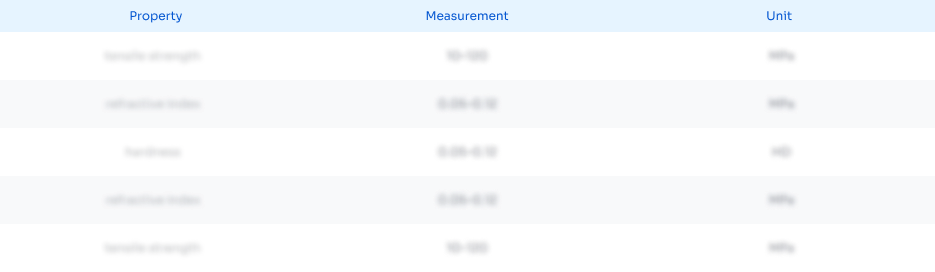
Abstract
Description
Claims
Application Information

- R&D
- Intellectual Property
- Life Sciences
- Materials
- Tech Scout
- Unparalleled Data Quality
- Higher Quality Content
- 60% Fewer Hallucinations
Browse by: Latest US Patents, China's latest patents, Technical Efficacy Thesaurus, Application Domain, Technology Topic, Popular Technical Reports.
© 2025 PatSnap. All rights reserved.Legal|Privacy policy|Modern Slavery Act Transparency Statement|Sitemap|About US| Contact US: help@patsnap.com