Plate form expansion feeding back closed-loop control system and method for cold continuous rolling machine
A technology of closed-loop control and cold tandem rolling mill, applied in the direction of contour control, metal rolling, etc., to achieve the effect of improving the shape quality of strip steel
- Summary
- Abstract
- Description
- Claims
- Application Information
AI Technical Summary
Problems solved by technology
Method used
Image
Examples
Embodiment Construction
[0030] According to Figure 2 ~ Figure 4 The preferred embodiments of the present invention are given and described in detail to make it easier to understand the structural and functional characteristics of the present invention, but they are not used to limit the scope of the present invention.
[0031] See now figure 2 , image 3 with Figure 4 , Will take the conventional tandem cold rolling mill composed of five stands as an example.
[0032] Such as figure 2 As shown, a flatness measuring device 1 (that is, a set of flatness measuring rolls) is installed after the final frame 7, that is, the fifth frame, to measure the shape of the actual strip steel. The actual plate shape curve is represented by a set of stresses in the width direction of the strip, namely
[0033] σ=[σ 1 σ 2 …Σ n ] T
[0034] Where σ i Is the stress at a certain point in the width direction of the strip (such as Figure 4 Shown). The flat shape target curve (determined by the process an...
PUM
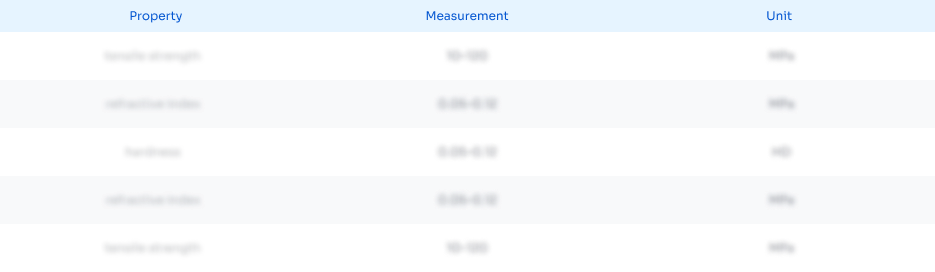
Abstract
Description
Claims
Application Information

- Generate Ideas
- Intellectual Property
- Life Sciences
- Materials
- Tech Scout
- Unparalleled Data Quality
- Higher Quality Content
- 60% Fewer Hallucinations
Browse by: Latest US Patents, China's latest patents, Technical Efficacy Thesaurus, Application Domain, Technology Topic, Popular Technical Reports.
© 2025 PatSnap. All rights reserved.Legal|Privacy policy|Modern Slavery Act Transparency Statement|Sitemap|About US| Contact US: help@patsnap.com