High-precision low-friction magnetic suspension sliding composite guid rail
A low-friction, high-precision technology applied to guide rails. It can solve the problems of unstable performance, high production cost, easy generation of vibration and noise, etc., and achieve the effect of strong load adaptability, anti-vibration ability, strong anti-vibration interference ability, and stable guiding performance.
- Summary
- Abstract
- Description
- Claims
- Application Information
AI Technical Summary
Problems solved by technology
Method used
Image
Examples
Embodiment
[0018] see figure 1 , the present embodiment is between the bottom end face of moving part 1 and the supporting surface of guide rail 2, a pair of bottom permanent magnet pair 4 is oppositely installed with the same sex, keeps the bottom end face of moving part 1 with the repulsive force that bottom permanent magnet pair 4 forms The supporting surfaces of the guide rail 2 are in a non-contact state, and a positive pressure is formed between the moving part 1 and the top guide surface 3 of the guide rail 2;
[0019] With one side end surface of the moving part 1 and the guide rail 2 as the side guide surface 5, on the other side end surface opposite to the side guide surface 5, the side permanent magnet pair 6 is installed oppositely with the same sex, and the side permanent magnet The repulsive force formed by the magnet pair 6 keeps the moving part 1 and the guide rail 2 in a non-contact state on the side end surface, and forms a positive pressure on the side guide surface 5 ...
PUM
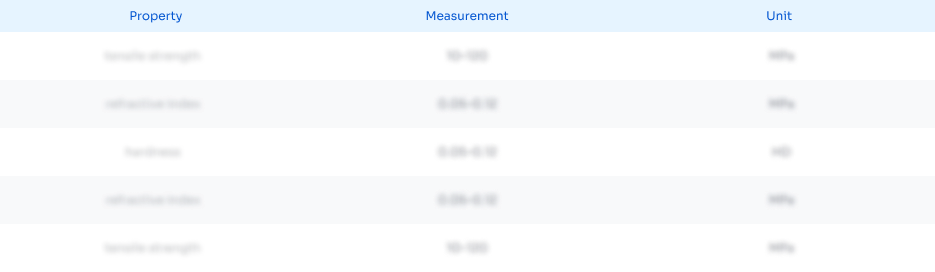
Abstract
Description
Claims
Application Information

- R&D
- Intellectual Property
- Life Sciences
- Materials
- Tech Scout
- Unparalleled Data Quality
- Higher Quality Content
- 60% Fewer Hallucinations
Browse by: Latest US Patents, China's latest patents, Technical Efficacy Thesaurus, Application Domain, Technology Topic, Popular Technical Reports.
© 2025 PatSnap. All rights reserved.Legal|Privacy policy|Modern Slavery Act Transparency Statement|Sitemap|About US| Contact US: help@patsnap.com