Secondary transformation technological method of high concentration carbon monooxide
A technology of carbon monoxide and process methods, applied in chemical instruments and methods, inorganic chemistry, non-metallic elements, etc., to achieve the effects of not being overheated, simple in construction, and easy in process equipment
- Summary
- Abstract
- Description
- Claims
- Application Information
AI Technical Summary
Problems solved by technology
Method used
Image
Examples
Embodiment 1
[0035] The 180,000-ton synthetic ammonia high-concentration CO secondary conversion process device designed by the present invention is used in a Shell coal gasification project with a coal input of 1,000 tons / day.
[0036] Process such as figure 1 As shown, the raw material gas from dry pulverized coal gasification is heated by the gas preheater 4 and the gas heat exchanger 5, and then supplemented with steam in the steam mixer 6, then enters the primary shift furnace 1 for shift reaction, and exits the primary shift furnace After the shift gas is quenched and cooled with chilled water in the 1# quenching filter 7, it enters the second-stage first-stage shift furnace 2 for shift reaction, and the shift gas exiting the second-stage first-stage shift furnace 2 passes through the methanation heater 8 to recover heat. The gas entering the primary converter 1 is heated in the gas heat exchanger 5, and after being quenched and cooled by quenching water in the 2# quenching filter 9,...
Embodiment 2
[0045] The 500,000-ton synthetic ammonia high-concentration CO secondary conversion process device designed by the invention is used in the Shell coal gasification project with a coal input of 2,400 tons / day.
[0046] Process such as figure 2 Shown: The feed gas from dry pulverized coal gasification is divided into two streams, one of which is preheated by the coal gas preheater 4, mixed with supplementary steam in the steam mixer 6, and then heat exchanged by the coal gas heat exchanger 5, and then further The first-stage shift furnace 1, the shift gas leaving the first-stage shift furnace 1 passes through the steam superheater 19 to recover heat, and after exchanging heat with the gas entering the first-stage shift furnace (first shift furnace) 1 in the gas heat exchanger 5, it is exchanged with the gas from the first stage shift furnace. The second raw material gas of dry pulverized coal gasification is mixed, and after being cooled by quenching water in 1# quenching filte...
PUM
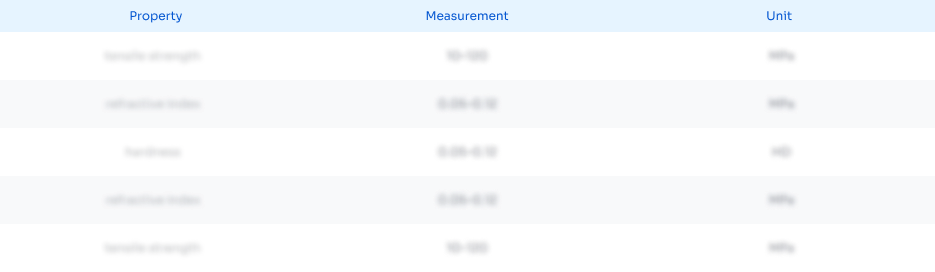
Abstract
Description
Claims
Application Information

- Generate Ideas
- Intellectual Property
- Life Sciences
- Materials
- Tech Scout
- Unparalleled Data Quality
- Higher Quality Content
- 60% Fewer Hallucinations
Browse by: Latest US Patents, China's latest patents, Technical Efficacy Thesaurus, Application Domain, Technology Topic, Popular Technical Reports.
© 2025 PatSnap. All rights reserved.Legal|Privacy policy|Modern Slavery Act Transparency Statement|Sitemap|About US| Contact US: help@patsnap.com