Method and apparatus for manufacturing vehicle parts
A technology for vehicle parts and components, applied in the direction of household components, transportation and packaging, applications, etc., can solve the problem of difficult placement of inserts, fixing elements and reinforcing elements, etc., to achieve the effect of improving flow characteristics
- Summary
- Abstract
- Description
- Claims
- Application Information
AI Technical Summary
Problems solved by technology
Method used
Image
Examples
Embodiment Construction
[0025] In the description made, identical or identical components have identical or identical reference numerals.
[0026] The exemplary embodiments shown in the drawings are shown for purposes of illustration only and are not to be considered as limiting in any way.
[0027] exist figure 1 In, a mold 50 is shown, which comprises a first part 51 and a second part 52, and in the second part 52 is provided a movable wall element 53 which can pass through figure 1 and 2 The arm 54 shown schematically in FIG. 2 is operated from the outside of the mold 50 . In the mold 50 , the recess forms a cavity 55 , a part of which is delimited by a movable wall element 53 . In the cavity 55 , a vehicle component 1 , for example a cover element, can be formed. When starting the injection molding operation, the movable wall element 53 is retracted in the first position, in other words, the space of the cavity 55 is relatively large and the plastic is introduced into the cavity 55 . Subsequ...
PUM
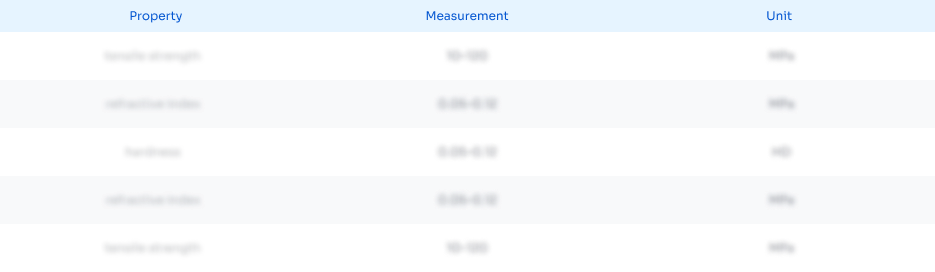
Abstract
Description
Claims
Application Information

- R&D
- Intellectual Property
- Life Sciences
- Materials
- Tech Scout
- Unparalleled Data Quality
- Higher Quality Content
- 60% Fewer Hallucinations
Browse by: Latest US Patents, China's latest patents, Technical Efficacy Thesaurus, Application Domain, Technology Topic, Popular Technical Reports.
© 2025 PatSnap. All rights reserved.Legal|Privacy policy|Modern Slavery Act Transparency Statement|Sitemap|About US| Contact US: help@patsnap.com