Plasma display device, plasma display panel and producing method
A display panel and display device technology, which is applied in the direction of AC plasma display panels, cold cathode manufacturing, electrode system manufacturing, etc., can solve the problems of no longer smooth interaction, poor image jumping characteristics, unstable discharge, etc., to prevent power Effects of loss, brightness enhancement, contrast characteristic improvement
- Summary
- Abstract
- Description
- Claims
- Application Information
AI Technical Summary
Problems solved by technology
Method used
Image
Examples
no. 1 approach
[0033] FIG. 5 is a perspective view showing a partition wall structure of the plasma display panel according to the first embodiment of the present invention. The following description will be made before looking at FIG. 5. Although not shown in the figure, the plasma display panel according to the first embodiment of the present invention is the same as the prior art. The substrates are bonded and formed at intervals.
[0034] The front substrate has sustain electrodes formed by pairing scan electrodes and sustain electrodes on the top of the front glass, and an upper dielectric layer is laminated on the front glass where the scan electrodes and sustain electrodes are arranged in parallel to limit the discharge current. In addition, a protective layer of evaporated magnesium oxide (MgO) is formed on the upper dielectric layer, and the protective layer is used to prevent damage to the upper dielectric layer due to sputtering (sputtering) generated during plasma discharge, and ...
no. 2 approach
[0043] Figure 6 It is a perspective view showing the partition wall structure of the plasma display panel in the second embodiment of the present invention. Although not shown in the drawings, the plasma display panel according to the second embodiment of the present invention has a structure corresponding to the structure of the plasma display panel according to the first embodiment of the present invention described above. However, the partition walls formed in the plasma display panel according to the second embodiment of the present invention are as follows: Figure 6 As shown, the lower dielectric layer 130b' on the back glass 200' is configured to be surrounded by row ribs (row rib, 210a') and column ribs (column rib, 210b') to separate the Well Type of discharge cells. ), wherein the row partition wall 210a' and the column partition wall 210b' have different heights from each other. In this case, the row partition walls 210a' and the column partition walls 210b' are ...
PUM
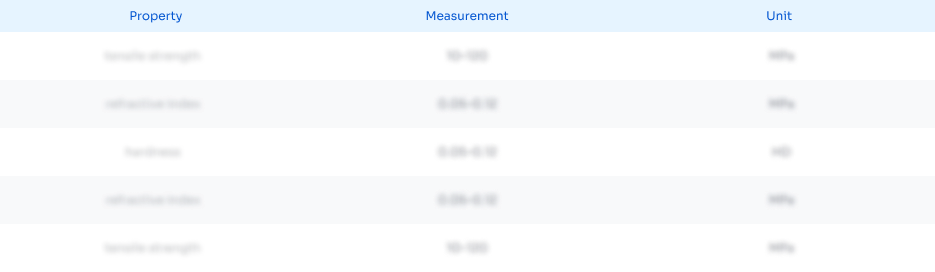
Abstract
Description
Claims
Application Information

- R&D
- Intellectual Property
- Life Sciences
- Materials
- Tech Scout
- Unparalleled Data Quality
- Higher Quality Content
- 60% Fewer Hallucinations
Browse by: Latest US Patents, China's latest patents, Technical Efficacy Thesaurus, Application Domain, Technology Topic, Popular Technical Reports.
© 2025 PatSnap. All rights reserved.Legal|Privacy policy|Modern Slavery Act Transparency Statement|Sitemap|About US| Contact US: help@patsnap.com