Hot-air furnace combined by combustion chamber and dustproof multi-stage heat exchanger with burning-resistant device
A hot blast stove and combustion chamber technology, applied in heating devices, lighting and heating equipment, dry gas arrangement, etc., can solve the problems of short life, undurable, unscientific, etc., achieve fast shutdown, low operation and maintenance costs, Automatically controls simple effects
- Summary
- Abstract
- Description
- Claims
- Application Information
AI Technical Summary
Problems solved by technology
Method used
Image
Examples
Embodiment Construction
[0027] The hot blast stove is composed of two parts: the first part is the combustion chamber (burner head), and the combustion chamber is made into a high-heat insulation combustion chamber according to the fuel provided. This part is to convert the fuel into high-temperature flue gas (500℃~ 1000°C) is supplied to the second heat exchanger assembly. The second part of the heat exchanger assembly is to convert the high-temperature flue gas from combustion into hot air at 150°C to 350°C through heat exchange, which can be directly mixed with the dried material and replaced for drying. This heat exchanger has undergone innovation and transformation, heat exchange with tubes, high-temperature flue gas in the tube, burn-resistant device, long practical life, multi-stage dust removal, and flue gas exhausted by simple treatment can fully meet the emission requirements, and has multiple safety features. The ventilation door ensures the safety of the heat exchanger during a power fail...
PUM
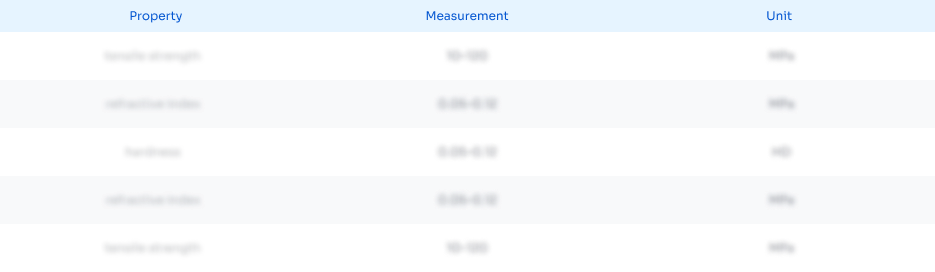
Abstract
Description
Claims
Application Information

- Generate Ideas
- Intellectual Property
- Life Sciences
- Materials
- Tech Scout
- Unparalleled Data Quality
- Higher Quality Content
- 60% Fewer Hallucinations
Browse by: Latest US Patents, China's latest patents, Technical Efficacy Thesaurus, Application Domain, Technology Topic, Popular Technical Reports.
© 2025 PatSnap. All rights reserved.Legal|Privacy policy|Modern Slavery Act Transparency Statement|Sitemap|About US| Contact US: help@patsnap.com