Force sensor based on Micro-Nano composite structure
A force sensor and combined structure technology, applied in the field of micro/nano electromechanical systems and sensing, can solve problems such as unsatisfactory physical properties of materials, and achieve the effects of small overall size, large deformation and good flexibility
- Summary
- Abstract
- Description
- Claims
- Application Information
AI Technical Summary
Problems solved by technology
Method used
Image
Examples
Embodiment Construction
[0023] The present invention will be further described in detail below in conjunction with the accompanying drawings and specific embodiments.
[0024] Such as figure 1 As shown, the force sensor includes a substrate 1, which is monocrystalline silicon. The substrate 1 is covered with an insulating layer 2, which can be made of silicon oxide or silicon nitride. The insulating layer 2 is provided with four electrodes facing each other in pairs, including an electrode 3 , an electrode 5 , an electrode 6 and an electrode 9 , and these electrodes are made of polysilicon material. The bridge beams 4 and 8 are respectively lapped on the corresponding counter electrodes, such as figure 1 As shown, the two ends of the bridge beam 4 are respectively fixed on the electrode 3 and the electrode 5, and the two ends of the bridge beam 8 are respectively fixed on the electrode 6 and the electrode 9.
[0025] The mass block 7 is made of polysilicon material, and the mass block 7 is fixed a...
PUM
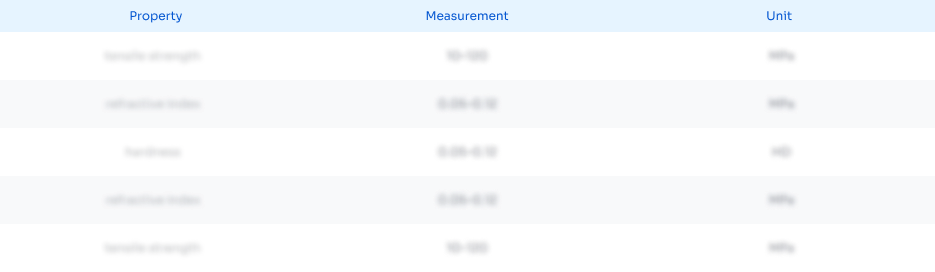
Abstract
Description
Claims
Application Information

- Generate Ideas
- Intellectual Property
- Life Sciences
- Materials
- Tech Scout
- Unparalleled Data Quality
- Higher Quality Content
- 60% Fewer Hallucinations
Browse by: Latest US Patents, China's latest patents, Technical Efficacy Thesaurus, Application Domain, Technology Topic, Popular Technical Reports.
© 2025 PatSnap. All rights reserved.Legal|Privacy policy|Modern Slavery Act Transparency Statement|Sitemap|About US| Contact US: help@patsnap.com