3-PPTTRS six freedom degree parallel precise jiggle robot
A degree of freedom, robot technology, applied in micro manipulators, manipulators, metal processing mechanical parts, etc., can solve problems such as no practical value, and achieve the effect of large linear and rotary motion range, large impact force, and high resolution.
- Summary
- Abstract
- Description
- Claims
- Application Information
AI Technical Summary
Problems solved by technology
Method used
Image
Examples
Embodiment Construction
[0021] The present invention will be further described below in conjunction with accompanying drawing:
[0022] The invention mainly includes five parts: a 3-PPTTRS mechanism, a flexible hinge pair, a static pressure screw mechanism, a hydraulic oil supply system, and an open numerical control system. The 3-PPTTRS mechanism of the present invention enables the system to input displacement through a simple linear movement pair 10, generate a larger stroke range, and can perform six-degree-of-freedom movements; in the same system, single-axis, double-axis and three-axis The degree of freedom flexible hinge pair is used as the kinematic pair in the 3-PPTTRS mechanism. By using the special structure of the flexible hinge, it avoids the error caused by the friction, clearance and backlash of the traditional kinematic pair; although the theory of static pressure technology is quite mature, but It is the first time to apply a high-precision static pressure screw mechanism to the fiel...
PUM
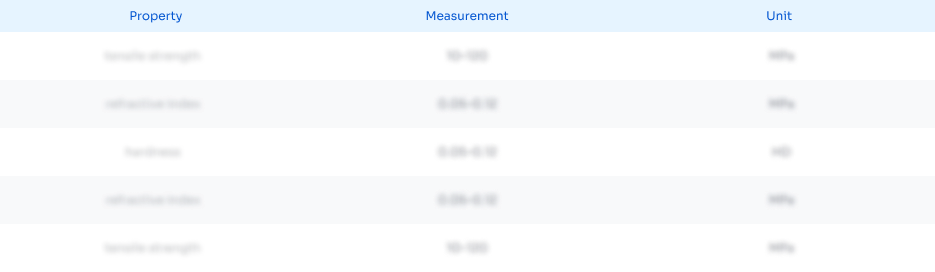
Abstract
Description
Claims
Application Information

- R&D
- Intellectual Property
- Life Sciences
- Materials
- Tech Scout
- Unparalleled Data Quality
- Higher Quality Content
- 60% Fewer Hallucinations
Browse by: Latest US Patents, China's latest patents, Technical Efficacy Thesaurus, Application Domain, Technology Topic, Popular Technical Reports.
© 2025 PatSnap. All rights reserved.Legal|Privacy policy|Modern Slavery Act Transparency Statement|Sitemap|About US| Contact US: help@patsnap.com