Method for manufacturing antifouling Batt-on-mesh press felt
A papermaking felt and a manufacturing method technology, which are applied in the directions of papermaking, papermaking, textiles, and papermaking, etc., can solve the problems of easily adhering felt fibers, blocking the pores of the felt, etc., and achieve the advantages of increased product added value, easy raw materials and low processing costs Effect
- Summary
- Abstract
- Description
- Claims
- Application Information
AI Technical Summary
Problems solved by technology
Method used
Image
Examples
Embodiment 1
[0010] Specifications of papermaking felt:
[0011] 47501 Single layer bottom mesh blanket.
[0012] Warp: φ0.2mm nylon monofilament × 6 strands; warp density: 100 threads / 10cm.
[0013] Weft: φ0.2mm nylon monofilament × 4 strands; weft density: 80 pcs / 10cm.
[0014] Texture: 1 / 3 broken twill.
[0015] Surface staple fiber: 17dtex nylon, 400g / m 2 . .
[0016] Core back staple fiber: 33dtex nylon, 100g / m 2 .
[0017] Needling density: 600 / cm 2 .
[0018] Acupuncture depth: 11-12mm.
[0019] Production process:
[0020] See figure 1 shown. Plying by monofilament, warp warp and weft winding, weaving and gray cloth setting; then opening, carding, cross-lapping and pre-needling by synthetic fibers; double-merging warp, acupuncture, cleaning, padding anti-fouling agent and pre-pressing , and become the finished product after being baked and dried.
[0021] Among them, the treatment agent formula:
[0022] Polytetrafluoroethylene 40g / L.
[0023] Melamine adhesive 0.8g...
Embodiment 2
[0030] Specifications of papermaking felt:
[0031] 47501 Single layer bottom mesh blanket.
[0032] Warp: φ0.2mm nylon monofilament × 6 strands; warp density: 100 threads / 10cm.
[0033] Weft: φφ0.2mm nylon monofilament × 4 strands; weft density: 80 pieces / 10cm.
[0034] Texture: 1 / 3 broken twill.
[0035] Surface staple fiber: 17dtex nylon, 400g / m 2 . .
[0036] Core back staple fiber: 33dtex nylon, 100g / m 2 .
[0037] Needling density: 600 / cm 2 .
[0038] Acupuncture depth: 11-12mm.
[0039] Production process:
[0040] See figure 1 shown. Plying by monofilament, warp warp and weft winding, weaving and gray cloth setting; then opening, carding, cross-lapping and pre-needling by synthetic fibers; double-merging warp, acupuncture, cleaning, padding anti-fouling agent and pre-pressing , and become the finished product after being baked and dried.
[0041] Among them, the treatment agent formula:
[0042] Polytetrafluoroethylene 55g / L.
[0043] Melamine adhesive ...
Embodiment 3
[0050] Specifications of papermaking felt:
[0051] 47501 Single layer bottom mesh blanket.
[0052] Warp: φ0.2mm nylon monofilament × 6 strands; warp density: 100 threads / 10cm.
[0053] Weft: φ0.2mm nylon monofilament × 4 strands; weft density: 80 pcs / 10cm.
[0054] Texture: 1 / 3 broken twill.
[0055] Surface staple fiber: 17dtex nylon, 400g / m 2 . .
[0056] Core back staple fiber: 33dtex nylon, 100g / m 2 .
[0057] Needling density: 600 / cm 2 .
[0058] Acupuncture depth: 11-12mm.
[0059] Production process:
[0060] See figure 1 shown. Plying by monofilament, warp warp and weft winding, weaving and gray cloth setting; then opening, carding, cross-lapping and pre-needling by synthetic fibers; double-merging warp, acupuncture, cleaning, padding anti-fouling agent and pre-pressing , and become the finished product after being baked and dried.
[0061] Treatment agent formula:
[0062] Polytetrafluoroethylene 50g / L.
[0063] Melamine adhesive 1g / L.
[0064] Prod...
PUM
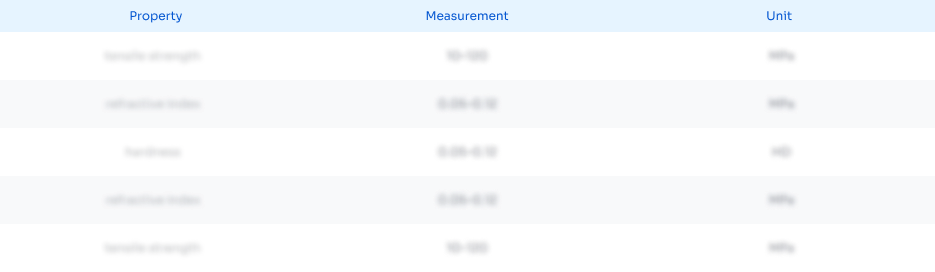
Abstract
Description
Claims
Application Information

- R&D
- Intellectual Property
- Life Sciences
- Materials
- Tech Scout
- Unparalleled Data Quality
- Higher Quality Content
- 60% Fewer Hallucinations
Browse by: Latest US Patents, China's latest patents, Technical Efficacy Thesaurus, Application Domain, Technology Topic, Popular Technical Reports.
© 2025 PatSnap. All rights reserved.Legal|Privacy policy|Modern Slavery Act Transparency Statement|Sitemap|About US| Contact US: help@patsnap.com