Catalyst of complexes of polymetal and multiple ligand, and preparation method
A multi-ligand and complex technology, applied in the field of preparing polyether, polyester and polyether polyol, can solve the problem that the high performance requirements of polyurethane cannot be met, the degree of unsaturation of polyether polyol is high, and the molecular weight of polyether polyol is limited. and other problems, to achieve the effect of good elasticity, high reaction speed and less monofunctional impurities
- Summary
- Abstract
- Description
- Claims
- Application Information
AI Technical Summary
Problems solved by technology
Method used
Examples
Embodiment 1
[0040] The preparation of catalyst 1, its preparation steps are:
[0041] 1. Take 13g of potassium hexacyanocobaltate and dissolve it in 130g of pure water to obtain solution 1 1 Get zinc chloride 40g, be dissolved in 120g pure water, get solution 2 1 ; Get 234g tert-butanol and 156g pure water to mix, get solution 3 1 ; Preparation concentration is 0.2wt% tributyl tin chloride (C 4 h 9 ) 3 Methanol solution of SnCl to obtain solution 4 1 Be 400 polyoxypropylene ethers (being called for short PPG-204) and 160g pure water ratio preparation solution 5 by 10g tert-butanol and 15g molecular weight 1 ;
[0042] 2. In a 2000ml reactor, add solution 1 1 , and then dropwise added solution 2 with stirring 1 , and then homogenize for 30 minutes after adding, then add solution 3 1 , and stirred for 1 hour, and finally added 24 g of solution 4 1 , and stirred for 3 hours. Vacuum filtration gave solid A 1 ;
[0043] 3rd, the solid A 1 Put into reaction vessel, add concentration...
Embodiment 2
[0046] The preparation of catalyst 2, its preparation steps are:
[0047] 1. Take 11g of potassium hexacyanoferrate and dissolve it in 88g of pure water to obtain solution 1 2 Get manganese chloride 43g, be dissolved in 65g pure water, get solution 2 2 ; Get 88g tert-amyl alcohol and 132g pure water to mix, get solution 3 2 ; Preparation concentration is 1.0wt% tributyl tin chloride (C 4 h 9 ) 3 Methanol solution of SnCl to obtain solution 4 2 ; Press 10g tert-butyl alcohol: 15g tert-butylamine: 160g purified water to prepare solution 5 2 ;
[0048] 2. In a 2000ml reactor, add solution 1 2 , and then dropwise added solution 2 with stirring 2 , and then homogenize for 60 minutes after adding, then add solution 3 2 , and stirred for 2 hours, and finally added 11 g of solution 4 2 , and stirred for 0.5 hours. Vacuum filtration gave solid A 2 ;
[0049] 3rd, the solid A 2 Put into reaction container, add concentration and be 80wt% tert-butanol aqueous solution 220g, ...
Embodiment 4
[0059] The preparation of catalyst 4, its preparation steps are:
[0060] 1. Take 12g of potassium hexacyanocobaltate and dissolve it in 100 grams of pure water to obtain solution 1 4 Get zinc bromide 42g, be dissolved in 90g pure water, get solution 2 4 ; Get 150g tert-butanol and 150g pure water and mix to get solution 3 4 ; Preparation concentration is 0.5wt% tributyl tin chloride (C 4 h 9 ) 3 Methanol solution of SnCl to obtain solution 4 4 ; Prepare solution 5 in the ratio of 10g tert-butyl alcohol and 15g dibutyl phthalate and 160g purified water 4 ;
[0061] 2. In a 2000ml reactor, add solution 1 4 , and then dropwise added solution 2 with stirring 4 , after adding, homogenize for 40 minutes, then add solution 3 4 , and stirred for 1.5 hours, and finally added 18 g of solution 4 4 , and stirred for 2 hours, vacuum filtered to obtain solid A 4 .
[0062] 3rd, the solid A 4 Put into reaction container, add concentration and be 70wt% tert-butanol aqueous solut...
PUM
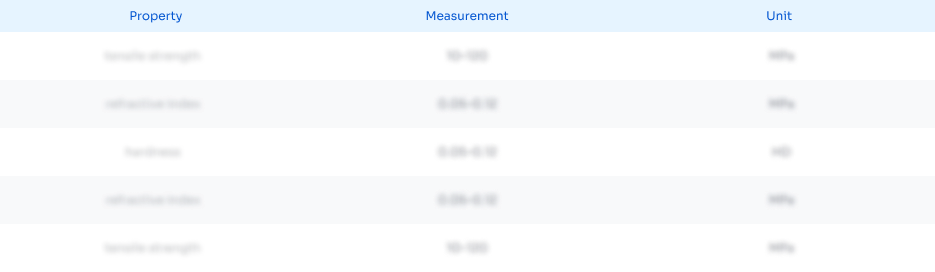
Abstract
Description
Claims
Application Information

- R&D Engineer
- R&D Manager
- IP Professional
- Industry Leading Data Capabilities
- Powerful AI technology
- Patent DNA Extraction
Browse by: Latest US Patents, China's latest patents, Technical Efficacy Thesaurus, Application Domain, Technology Topic, Popular Technical Reports.
© 2024 PatSnap. All rights reserved.Legal|Privacy policy|Modern Slavery Act Transparency Statement|Sitemap|About US| Contact US: help@patsnap.com