Methacrylates as stabilizers for polymer polyols
A methyl and compound technology, applied in the field of macromonomers
- Summary
- Abstract
- Description
- Claims
- Application Information
AI Technical Summary
Problems solved by technology
Method used
Image
Examples
preparation example Construction
[0161] The combination of conditions selected for the preparation of the pre-stabilizer should not result in the formation of crosslinks or gels in the pre-stabilizer which could adversely affect the final properties in preparing the polymer polyol composition. The combination of too low diluent concentration, too high precursor and / or monomer concentration, too high catalyst concentration, too long reaction time, and too many unsaturated bonds in the precursor will result in crosslinking or gelling leading to ineffective preformed stabilizers.
[0162] Particularly preferred methods of preparing the preformed stabilizers of the present invention include, for example, those described in US Patent Nos. 5,196,476 and 6,013,731, the disclosures of which are incorporated herein by reference. Preferred diluents and relative concentrations, ethylenically unsaturated monomers and relative concentrations, free radical initiators and relative concentrations, and reaction conditions are...
Embodiment 1-5
[0228]The examples in this series relate to the preparation of polymer polyols made from preformed stabilizers I-V respectively. The individual polymer polyols were prepared in a two-stage reaction system comprising a continuous stirred tank reactor (CSTR) (first stage) equipped with an impeller and 4 baffles and a plug flow reactor (second stage). The residence time in each reactor was about 60 minutes. The reactants are well mixed by being continuously pumped into the reactor from the feed tank through the in-line static mixer and then through the feed tube. The temperature of the reaction mixture was controlled at 115±1°C. The product from the second stage reactor was continuously overflowed through a pressure regulator designed to control the pressure in each stage at 45 psig. The polymer polyol then passes through a cooler and into a collector. The crude product was vacuum stripped to remove volatiles. The total polymer wt% in the product is calculated from the monome...
Embodiment 6-7
[0231] These examples relate to the preparation of free rise foams from commercially available polymer polyols as well as the polymer polyol prepared in Example 4.
[0232] The polymer polyol, amine catalyst and silicone surfactant were added to a 1.5 gallon baffled cylindrical paper container. The materials were mixed for 60 seconds at 2400 rpm using an agitator with two turbine impellers. The mixture was then degassed for 10 seconds. After degassing, the tin catalyst was added and the batches were mixed for 10 seconds at 2400 rpm. While the mixer was still spinning, add the toluene diisocyanate and mix the batch for 5 seconds. The mixture was then poured into 14 x 14 x 6 inch cardboard boxes where it rose freely until the reaction was complete. The foam was then heated in an oven at 225°C for 5 minutes. Foam properties were determined according to ASTM standard D-3574-66. The parameters used in the experiments are listed in Table 3.
[0233] parameters
[023...
PUM
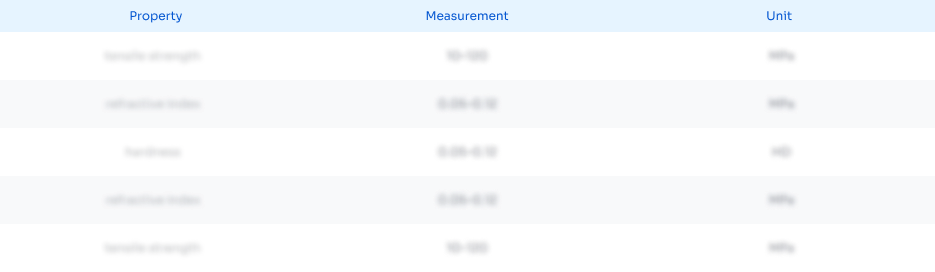
Abstract
Description
Claims
Application Information

- R&D
- Intellectual Property
- Life Sciences
- Materials
- Tech Scout
- Unparalleled Data Quality
- Higher Quality Content
- 60% Fewer Hallucinations
Browse by: Latest US Patents, China's latest patents, Technical Efficacy Thesaurus, Application Domain, Technology Topic, Popular Technical Reports.
© 2025 PatSnap. All rights reserved.Legal|Privacy policy|Modern Slavery Act Transparency Statement|Sitemap|About US| Contact US: help@patsnap.com