Manufacture of active magnesium oxide
A kind of technology of active magnesium oxide and manufacturing method, applied in the field of inorganic chemical industry
- Summary
- Abstract
- Description
- Claims
- Application Information
AI Technical Summary
Problems solved by technology
Method used
Image
Examples
Embodiment 1
[0024] As shown in Figure 1, after beneficiation, the natural hydromagnesite is crushed with a jaw crusher to a particle size of less than 40mm, and then crushed with a Raymond mill to a particle size of less than 100 mesh, and the obtained hydromagnesite powder is added to the rotary kiln , keep the kiln temperature at 550°C, and the material stays in the kiln for 60 minutes. The magnesia coming out of the kiln is naturally cooled and crushed to 325 mesh with a mechanical pulverizer to obtain active magnesia with an iodine adsorption value of 98mgI / g and a magnesia content of 93.6%.
Embodiment 2
[0026] After beneficiation, the natural hydromagnesite is crushed with a jaw crusher to a particle size of less than 40mm, and then crushed to 100 mesh with a Raymond mill. The obtained hydromagnesite powder is added to a rotary kiln, and the kiln temperature is kept at 450°C. Stay in the kiln for 120 minutes. The magnesia coming out of the kiln is naturally cooled and crushed to 325 meshes with a mechanical pulverizer to obtain active magnesia with an iodine adsorption value of 119 mgI / g and a magnesia content of 91.8%.
Embodiment 3
[0028] After the natural hydromagnesite is beneficiated, it is crushed with a jaw crusher to a particle size of less than 40mm, and then crushed to 100 mesh with a Raymond mill. Stay in the kiln for 30 minutes. The magnesia coming out of the kiln is naturally cooled and crushed to 325 mesh with a mechanical pulverizer to obtain active magnesia with an iodine adsorption value of 81.8mgI / g and a magnesia content of 95.2%.
PUM
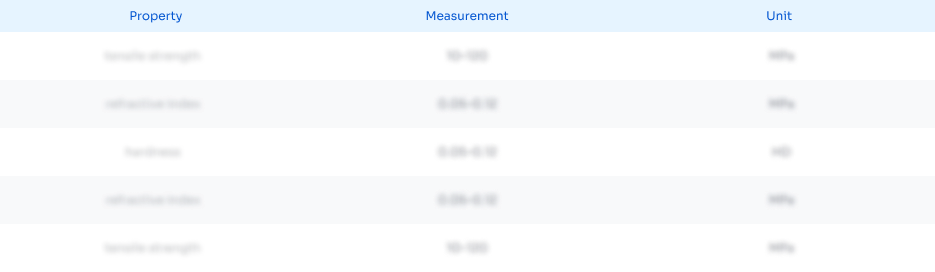
Abstract
Description
Claims
Application Information

- Generate Ideas
- Intellectual Property
- Life Sciences
- Materials
- Tech Scout
- Unparalleled Data Quality
- Higher Quality Content
- 60% Fewer Hallucinations
Browse by: Latest US Patents, China's latest patents, Technical Efficacy Thesaurus, Application Domain, Technology Topic, Popular Technical Reports.
© 2025 PatSnap. All rights reserved.Legal|Privacy policy|Modern Slavery Act Transparency Statement|Sitemap|About US| Contact US: help@patsnap.com