Linen blend yarn and producing method thereof
A production method and technology of hemp blending
- Summary
- Abstract
- Description
- Claims
- Application Information
AI Technical Summary
Problems solved by technology
Method used
Examples
Embodiment 1
[0011] Select 50 kg of flax and its cotton fiber, mix with 50 kg of soluble vinylon, go through cleaning, carding, drawing, roving, spun yarn, winding, warping, sizing, weaving, desizing, dedimensionalizing, singeing, Processes such as bleaching, tentering and drying complete the production of the fabric. In the dimension removal process, use a dyeing jigger, run 10 times in 450 liters of penetrant EC aqueous solution, wash twice in 450 liters of water at 100°C, go through 3 times each time, and finally wash in cold water once to complete the dimension removal process.
Embodiment 2
[0013] Select 55 kg of flax and chemical fiber, mix with 45 kg of soluble vinylon, and then go through cleaning, carding, drawing, roving, spun yarn, winding, warping, sizing, weaving, desizing, fiber removal, singeing, bleaching , stentering and drying processes to complete the production of fabrics. In the dimension removal process, use a dyeing jigger, run 12 times in 450 liters of penetrant EC aqueous solution, wash 3 times in 450 liters of water at 100°C, go 3 times each time, and finally wash in cold water once to complete the dimension removal process.
Embodiment 3
[0015] Select 60 kg of flax and viscose fiber, mix 40 kg of soluble vinylon, go through cleaning, carding, drawing, roving, spun yarn, winding, warping, sizing, weaving, desizing, dedimensionalizing, singeing, Processes such as bleaching, tentering and drying complete the production of the fabric. In the dimension removal process, use a dyeing jigger, run 15 times in 450 liters of penetrant EC aqueous solution, wash 5 times in 450 liters of water at 100°C, go through 5 times each time, and finally wash in cold water once to complete the dimension removal process.
PUM
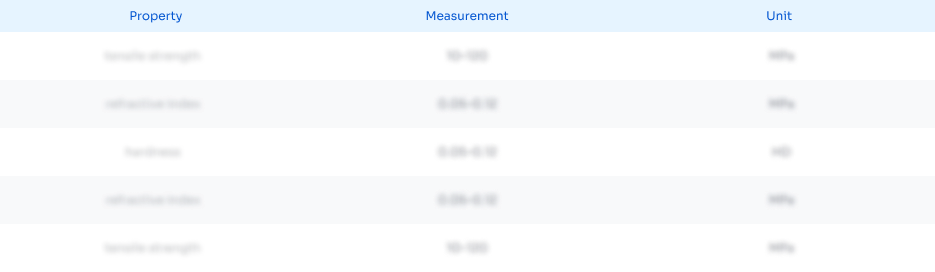
Abstract
Description
Claims
Application Information

- Generate Ideas
- Intellectual Property
- Life Sciences
- Materials
- Tech Scout
- Unparalleled Data Quality
- Higher Quality Content
- 60% Fewer Hallucinations
Browse by: Latest US Patents, China's latest patents, Technical Efficacy Thesaurus, Application Domain, Technology Topic, Popular Technical Reports.
© 2025 PatSnap. All rights reserved.Legal|Privacy policy|Modern Slavery Act Transparency Statement|Sitemap|About US| Contact US: help@patsnap.com