T-shape joint double light beam laser synchronous welding method and device
A laser welding and double-beam technology, applied in laser welding equipment, welding equipment, metal processing equipment, etc., can solve problems such as weld defects, achieve high welding efficiency, convenient adjustment, and the effect of controlling stress and deformation
- Summary
- Abstract
- Description
- Claims
- Application Information
AI Technical Summary
Problems solved by technology
Method used
Image
Examples
Embodiment Construction
[0025] Embodiments of the present invention refer to the above drawings. Generally, the traditional method of splitting a laser beam into two laser beams by using a half-mirror or a beam-splitting prism is suitable for the above-mentioned purpose in principle. However, the half mirror is generally suitable for splitting the light of YAG laser, while the beam splitting prism is not suitable for high power CO 2 Laser beam splitting, because the top of the prism may be melted and damaged when the high-power laser is irradiated. And what the beam splitter in the present invention adopts is the metal reflector, because the excellent thermal conductivity of metal and the high reflectivity to laser beam, make the metal reflector can bear the laser beam of higher power density. Not only that, the good cooling of the metal mirror can eliminate the negative effect caused by uneven heating that is easily produced by the half-transparent mirror or the beam-splitting prism, so the metal m...
PUM
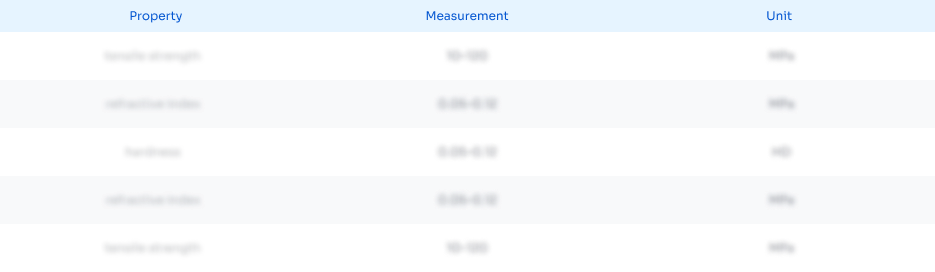
Abstract
Description
Claims
Application Information

- R&D Engineer
- R&D Manager
- IP Professional
- Industry Leading Data Capabilities
- Powerful AI technology
- Patent DNA Extraction
Browse by: Latest US Patents, China's latest patents, Technical Efficacy Thesaurus, Application Domain, Technology Topic, Popular Technical Reports.
© 2024 PatSnap. All rights reserved.Legal|Privacy policy|Modern Slavery Act Transparency Statement|Sitemap|About US| Contact US: help@patsnap.com