Micro-ball iron-based catalyst for Fischer-Tropsch synthesis and its preparation and use
An iron-based catalyst, Fischer-Tropsch synthesis technology, applied in the direction of catalyst activation/preparation, physical/chemical process catalyst, metal/metal oxide/metal hydroxide catalyst, etc. , poor sphericity, rough catalyst surface, etc., to achieve the effect of high anti-wear index, good sphericity, and simple preparation method
- Summary
- Abstract
- Description
- Claims
- Application Information
AI Technical Summary
Problems solved by technology
Method used
Examples
Embodiment 1
[0033] Get 15.2KgFe(NO3)3.9H2O, 0.10KgCe(NO3)3.6H2 and 0.26KgCu(CH3COO)2.H2O are added to 35L deionized water to obtain a mixed solution containing iron, cerium and copper. Take 6.15KgNa 2 CO 3Dissolve in 10L deionized water to obtain sodium carbonate solution, heat the above two solutions in a water bath to 70°C, then use an acid-resistant pump and an alkali-resistant pump to continuously drive the mixed salt solution and sodium carbonate solution into a vigorously stirred reaction tank and Keep the temperature at 70°C and pH=8.5-9.0 for precipitation. After the precipitation is completed, let it stand for aging for 1.5 hours, filter it with suction, wash it repeatedly with deionized water, and then beat again. 0.16KgK 2 C 2 o 4 2H 2 O was added to 10L of deionized water to obtain a solution, and 2.63Kg of silica sol with a concentration of 20wt% was added to the solution, and the mixed solution was obtained by stirring thoroughly. After heating to 70°C, it was added to ...
Embodiment 2
[0035] Take 32.03KgFe (NO 3 ) 3 9H 2 O, 0.04KgCe(NO 3 ) 3 ·6H 2 O and 0.83KgCu(CH 3 COO) 2 ·H 2 O is added to 35L deionized water to obtain a mixed solution containing iron, cerium and copper, and 13.06KgNa 2 CO 3 Dissolve in 20L deionized water to obtain sodium carbonate solution, heat the above two solutions in a water bath to 60°C, then use an acid-resistant pump and an alkali-resistant pump to continuously pump the mixed salt solution and sodium carbonate solution into a vigorously stirred reaction tank and Keep the temperature at 60°C, pH=9.5-10.0, and carry out precipitation. After the precipitation is completed, let it stand for aging for 3 hours, filter it with suction, wash it repeatedly with deionized water, and then beat again. 0.11KgK 2 C 2 o 4 2H 2 O was added to 15L deionized water to obtain a solution, and 6.20Kg of silica sol with a concentration of 25wt% was added to the solution, and the obtained mixed solution was fully stirred. After heating t...
Embodiment 3
[0037] Take 58.41KgFe (NO 3 ) 3 9H 2 O, 1.00KgCe(NO 3 ) 3 ·6H 2 O and 2.54KgCu(CH 3 COO) 2 ·H 2 O is added to 45L deionized water to obtain a mixed solution containing iron, cerium and copper, and 24.70KgNa 2 CO 3 Dissolve in 25L deionized water to obtain sodium carbonate solution, heat the above two solutions in a water bath to 80°C, then use an acid-resistant pump and an alkali-resistant pump to continuously pump the mixed salt solution and sodium carbonate solution into a vigorously stirred reaction tank and Keep the temperature at 80°C, pH=9.0-9.5, and carry out precipitation. After the precipitation is completed, let it stand for aging for 5 hours, filter it with suction, wash it repeatedly with deionized water, and beat it again for later use. 1.25Kg K 2 C 2 o 4 2H 2 O was added to 20L deionized water to obtain a solution, and 8.07Kg of silica sol with a concentration of 15wt% was added to the solution, and the obtained mixed solution was fully stirred. Aft...
PUM
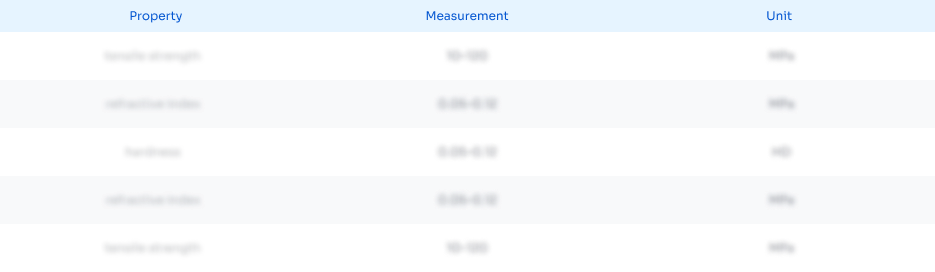
Abstract
Description
Claims
Application Information

- R&D Engineer
- R&D Manager
- IP Professional
- Industry Leading Data Capabilities
- Powerful AI technology
- Patent DNA Extraction
Browse by: Latest US Patents, China's latest patents, Technical Efficacy Thesaurus, Application Domain, Technology Topic, Popular Technical Reports.
© 2024 PatSnap. All rights reserved.Legal|Privacy policy|Modern Slavery Act Transparency Statement|Sitemap|About US| Contact US: help@patsnap.com