Construction optical visual sense transducer calibration method based on plane targets
A technology of visual sensor and calibration method, which is applied in the field of measurement, can solve problems such as difficult maintenance, difficult implementation, and difficulty in obtaining high-quality calibration images, and achieve the effects of improving calibration accuracy, reducing labor intensity, and simplifying the calibration process
- Summary
- Abstract
- Description
- Claims
- Application Information
AI Technical Summary
Problems solved by technology
Method used
Image
Examples
Embodiment
[0081] The actual design of the laser vision sensor is as follows: Figure 5 shown. Figure 5 It is the physical picture of the laser vision sensor installed on site. Figure 5 Among them, 6 is the sensor power line and output signal interface terminal, 7 is the CCD camera window, 8 is the sensor installation mechanism, 9 is the sensor housing, and 10 is the laser projector window.
[0082] Following the steps described above, use the figure 1 The planar calibration target shown calibrates the CCD camera and the structured light vision sensor. Targets at two positions are used to calibrate the structural parameters of the sensor, and the part of the calibration image such as Image 6 , 7 as shown, Figure 8 is the global world coordinates of the marked feature points on the obtained light plane, Figure 9 is the normalized image coordinates of the marked feature points on the light plane. The obtained calibration parameters are:
[0083] Camera internal parameters: ...
PUM
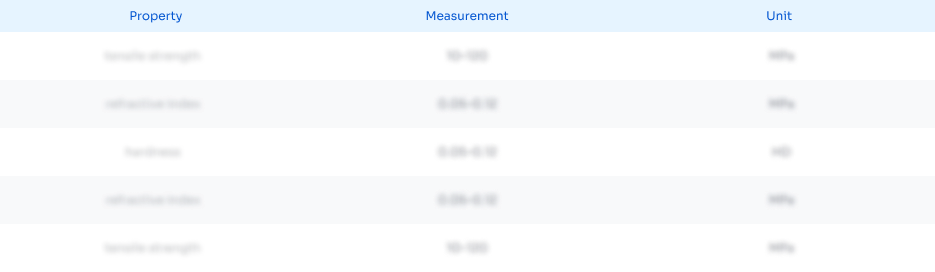
Abstract
Description
Claims
Application Information

- Generate Ideas
- Intellectual Property
- Life Sciences
- Materials
- Tech Scout
- Unparalleled Data Quality
- Higher Quality Content
- 60% Fewer Hallucinations
Browse by: Latest US Patents, China's latest patents, Technical Efficacy Thesaurus, Application Domain, Technology Topic, Popular Technical Reports.
© 2025 PatSnap. All rights reserved.Legal|Privacy policy|Modern Slavery Act Transparency Statement|Sitemap|About US| Contact US: help@patsnap.com