Method and apparatus for forming special-shaped wire material
A forming device and forming method technology, applied in metal rolling and other directions, can solve the problem that the number of forming times cannot be reduced, and achieve the effect of reducing the number of forming times and increasing the filling rate
- Summary
- Abstract
- Description
- Claims
- Application Information
AI Technical Summary
Problems solved by technology
Method used
Image
Examples
Embodiment
[0065] Using the molding device for the shaped wire with the above structure, mass production molding of shaped piston rings with cross-sectional shapes as shown in Fig. 8 was carried out from 0.65C-13Cr steel. During molding, the tension of the molded material between the front Turkic head 16 and the rear Turkic head 17 is controlled to be about 200N, and the tension between the molding unit 15 and the final processing Turkic head 21 is about 100N.
[0066] As a result, there was no annealing between the two moldings, and a high-precision finished product with a dimensional accuracy of 10 μm in the edge dimension H and the width W was obtained.
[0067] In the case of using a conventional device to manufacture the special-shaped piston ring in the shape of this embodiment, three non-driven Turk heads arranged in front and rear (tandem) are required for drawing forming. Moreover, drawing must be divided into three times, and intermediate annealing must be carried out twice in ...
PUM
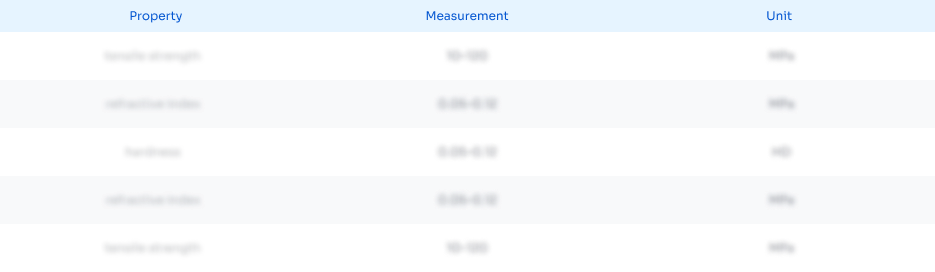
Abstract
Description
Claims
Application Information

- R&D
- Intellectual Property
- Life Sciences
- Materials
- Tech Scout
- Unparalleled Data Quality
- Higher Quality Content
- 60% Fewer Hallucinations
Browse by: Latest US Patents, China's latest patents, Technical Efficacy Thesaurus, Application Domain, Technology Topic, Popular Technical Reports.
© 2025 PatSnap. All rights reserved.Legal|Privacy policy|Modern Slavery Act Transparency Statement|Sitemap|About US| Contact US: help@patsnap.com