Method for metal type cast radiator and mould
A radiator and metal mold technology, applied in methods and molds, using metal molds to cast radiators, can solve the problems of center shrinkage, long modification cycle, uneven surface height, large heat dissipation area, short replacement cycle, well-structured effect
- Summary
- Abstract
- Description
- Claims
- Application Information
AI Technical Summary
Problems solved by technology
Method used
Image
Examples
Embodiment Construction
[0016] In the figure, a mold used in a low-pressure pouring radiator method is mainly composed of a side mold 1 and a mold bottom plate 2. The top of the side mold 1 is covered with a sprue cup 9, and the bottom of the cup mouth is a flow channel 14, and the flow channel Below 14 is the riser 10, and the mold bottom plate 2 is connected with an adjustable pad 5 through the adjustment screw 3, and the adjustable space 4 is between the adjustable pad 5 and the mold bottom plate 2, and a metal clip 12 is placed on it, and the metal clip The thickness of the sheet 12 is 13 to form the pitch of the cooling tooth sheet. The space between the top of the metal clip 12 and the riser 10 is the pouring space 11. The side mold 1 is connected to the fixed seat 7 on the mold bottom plate 2 through the screw rod 6 , The end of the screw mandrel 6 is provided with a handle 8 .
PUM
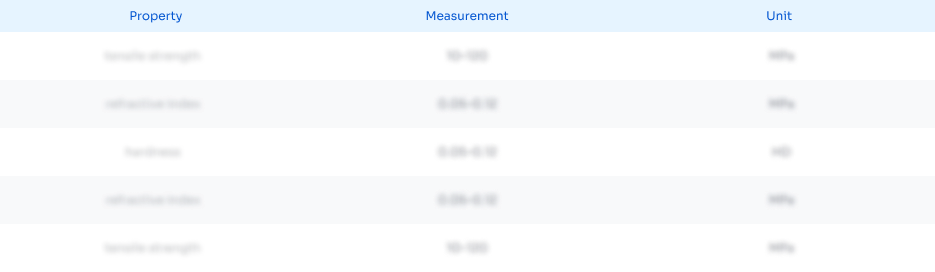
Abstract
Description
Claims
Application Information

- R&D
- Intellectual Property
- Life Sciences
- Materials
- Tech Scout
- Unparalleled Data Quality
- Higher Quality Content
- 60% Fewer Hallucinations
Browse by: Latest US Patents, China's latest patents, Technical Efficacy Thesaurus, Application Domain, Technology Topic, Popular Technical Reports.
© 2025 PatSnap. All rights reserved.Legal|Privacy policy|Modern Slavery Act Transparency Statement|Sitemap|About US| Contact US: help@patsnap.com