Large tilt rotary kiln cement calcining process and rotary kiln
A rotary kiln and inclination technology, used in cement production, rotary drum furnaces, furnaces, etc., can solve the problems of uneven cooling, reduce the strength and grindability of clinker, and incomplete combustion of fuel, and increase the effective mineral content. , the response is sufficient, the effect of promoting absorption
- Summary
- Abstract
- Description
- Claims
- Application Information
AI Technical Summary
Problems solved by technology
Method used
Image
Examples
Embodiment Construction
[0015] Embodiment of the present invention: first use traditional technology to make black raw material balls, the material balls are put into the kiln body (1) through the feeding pipe (7), and the kiln body (1) is in the speed reduction mechanism (4), the transmission gear (5) is driven to rotate, and the pellets are turned in the preheating zone a with the operation of the kiln, and the waste gas discharged from the firing zone b enters the preheating zone a to dry, preheat, dehydrate and carbonize the pellets The salt decomposes; the material balls then enter the firing zone b; during the combustion process, they are still continuously turned and displaced. When the temperature of the firing zone b reaches 1450 ° C, the material undergoes solid-phase and liquid-phase chemical reactions to form cement clinker minerals , the fired clinker descends and rolls into the cooling zone c; the normal temperature and high pressure air blown in by the central air duct shaft (3) perform...
PUM
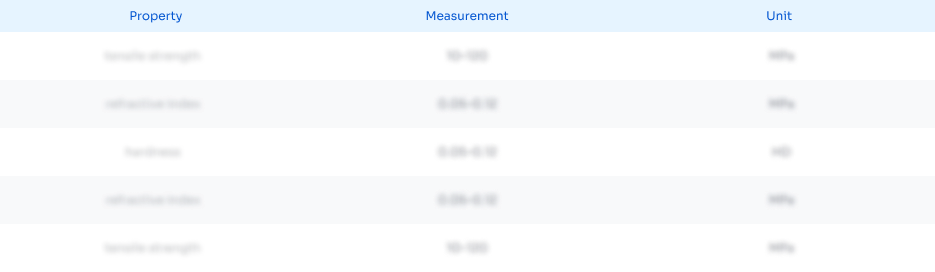
Abstract
Description
Claims
Application Information

- R&D Engineer
- R&D Manager
- IP Professional
- Industry Leading Data Capabilities
- Powerful AI technology
- Patent DNA Extraction
Browse by: Latest US Patents, China's latest patents, Technical Efficacy Thesaurus, Application Domain, Technology Topic, Popular Technical Reports.
© 2024 PatSnap. All rights reserved.Legal|Privacy policy|Modern Slavery Act Transparency Statement|Sitemap|About US| Contact US: help@patsnap.com