Device and method for mfg. GaN base
A substrate and heating device technology, applied in chemical instruments and methods, crystal growth, polycrystalline material growth, etc., can solve problems such as GaN substrate bending, GaN substrate cracks, sapphire substrate fracture, etc.
- Summary
- Abstract
- Description
- Claims
- Application Information
AI Technical Summary
Problems solved by technology
Method used
Image
Examples
no. 1 example
[0027] figure 1 An apparatus for manufacturing a GaN substrate according to a first embodiment of the present invention is shown.
[0028] The device for manufacturing a GaN substrate according to the first embodiment of the present invention is characterized in that the substrate is separated from the GaN layer by performing a laser lift-off process in the same chamber without transferring the substrate grown thereon. GaN layer substrate.
[0029] see figure 1 According to the first embodiment of the present invention, the device for manufacturing a GaN substrate includes: a chamber 11 for loading a substrate 100 in the chamber; a heating device 12 installed on the outside of the chamber 11 for The chamber 11 is heated to a high temperature of at least 1000° C.; a Ga carrier 14 is installed in the chamber 11 for containing GaN powder, Ga powder, or a mixed powder 13 composed of GaN and Ga, for making Ga by heating Molecular sublimation; injection pipe 15, injecting N into ...
no. 2 example
[0036] figure 2 A cross-sectional view of an apparatus for manufacturing a GaN substrate according to a second embodiment of the present invention is shown.
[0037] The device for manufacturing a GaN substrate according to the second embodiment of the present invention is characterized in that a GaN layer is grown on a substrate, the bottom surface of which is set to face the transparent window hole, by performing a laser in the same chamber Lifting process, which can separate the substrate and GaN layer from each other.
[0038] see figure 2 According to the second embodiment of the present invention, the device for manufacturing a GaN substrate includes: a chamber 21 for loading a substrate 100 in the chamber; a heating device 22 installed on the outside of the chamber 21 for The chamber 21 is heated to a high temperature of at least 1000° C.; the Ga carrier 24 is installed in the chamber 21 for accommodating GaN powder, Ga powder, or a mixed powder 23 composed of GaN a...
no. 3 example
[0046] image 3 A cross-sectional structure of an apparatus for manufacturing a GaN substrate according to a third embodiment of the present invention is shown.
[0047] see image 3 , the GaN substrate manufacturing apparatus according to the third embodiment of the present invention includes: a chamber 31 for loading a substrate 100 in the chamber; a heating device 32 installed outside the chamber 31 for heating the chamber 31 to a high temperature of at least 1000° C.; a Ga carrier 34 installed in a chamber 31 for containing GaN powder, Ga powder, or a mixed powder 33 composed of GaN and Ga, so that Ga molecules are sublimated by heating; an injection tube 35, spray N into the chamber 31 2 , NH 3 gas, so that the GaN layer 200 is grown on the substrate 100 by chemically reacting the nitrogen molecules with the Ga molecules sublimated from the Ga carrier 34; the exhaust pipe 36 is used to discharge the gas in the chamber 31 to the outside world; the transparent window ho...
PUM
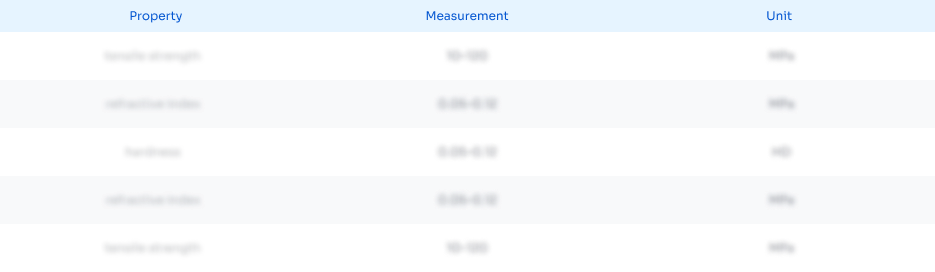
Abstract
Description
Claims
Application Information

- R&D
- Intellectual Property
- Life Sciences
- Materials
- Tech Scout
- Unparalleled Data Quality
- Higher Quality Content
- 60% Fewer Hallucinations
Browse by: Latest US Patents, China's latest patents, Technical Efficacy Thesaurus, Application Domain, Technology Topic, Popular Technical Reports.
© 2025 PatSnap. All rights reserved.Legal|Privacy policy|Modern Slavery Act Transparency Statement|Sitemap|About US| Contact US: help@patsnap.com