Current associating and unloading control method for multiple-pump hydraulic system
A hydraulic system and control method technology, applied in fluid pressure actuators, servo motor components, mechanical equipment, etc., can solve the problems of reducing system and component reliability, system reliability and life damage, and large temperature rise of hydraulic systems , to make full use of engine power, reduce energy consumption and temperature rise, and increase energy consumption
- Summary
- Abstract
- Description
- Claims
- Application Information
AI Technical Summary
Problems solved by technology
Method used
Image
Examples
Embodiment Construction
[0015] The present invention will be further described below in conjunction with accompanying drawing.
[0016] figure 1 Among them, the two-position two-way valve 2 is connected in parallel between the main pump 1 and the auxiliary pump 3, the one-way valve 4 is connected in series between the main pump 1 and the two-position two-way valve 2, and the control oil circuit of the two-position two-way valve 2 The electromagnetic reversing valve 6 is connected in series, and the electromagnetic reversing valve is controlled by the control switch 5 . The control switch is normally open, and the confluence control pressure makes the main pump and auxiliary pump confluence. When the load pressure of the main pump reaches the set unloading pressure of the auxiliary pump, the control switch is closed by the signal of the pressure sensor (after amplification), the electromagnetic reversing valve is disconnected, and the control oil circuit of the two-position two-way valve 2 is cut off...
PUM
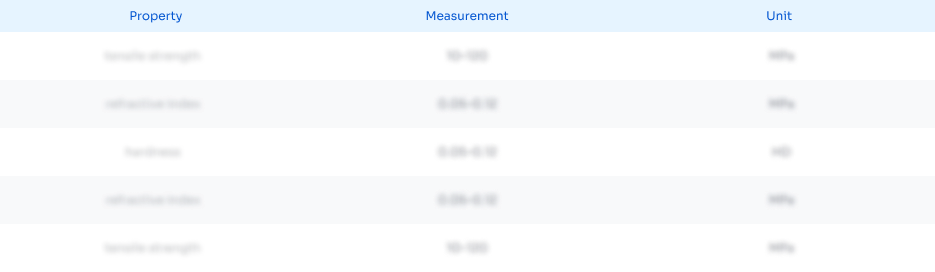
Abstract
Description
Claims
Application Information

- R&D
- Intellectual Property
- Life Sciences
- Materials
- Tech Scout
- Unparalleled Data Quality
- Higher Quality Content
- 60% Fewer Hallucinations
Browse by: Latest US Patents, China's latest patents, Technical Efficacy Thesaurus, Application Domain, Technology Topic, Popular Technical Reports.
© 2025 PatSnap. All rights reserved.Legal|Privacy policy|Modern Slavery Act Transparency Statement|Sitemap|About US| Contact US: help@patsnap.com