Method for producing yeast powder by using beer waste yeast
A technology for beer waste yeast and yeast powder, applied in the application, animal feed, fungi and other directions, can solve the problems of high water content of yeast mud, reduced use value, difficult to scale production, etc. Guaranteed quality effect
- Summary
- Abstract
- Description
- Claims
- Application Information
AI Technical Summary
Problems solved by technology
Method used
Examples
Embodiment 1
[0017] Take 100Kg of yeast sludge, add 5Kg of starch and 0.25Kg of yeast medium, stir and aerate the material to form a slurry, after 10 hours, heat up to 26°C, the number of cells under the microscope is 1 billion / g, and the number of living cells is more than 70%. After activation The yeast is directly used as the strain of solid fermentation.
[0018] 100Kg of soybean meal, 50Kg of bean dregs and 30Kg of beer dregs as fermentation raw materials are used as main ingredients, mixed with activated yeast, so that the water content is 58%, and the inoculum amount of yeast is 1 billion / g. At the same time, add inorganic nutrient salts, mix and stir evenly, then pile up and ferment. Potassium 0.07%. The thickness of the fermented materials can be piled up to 20cm. When the temperature rises above 40°C, turn over the materials and ventilate to lower the temperature. The temperature is controlled at 30°C, and the fermentation time is 36h. When the fermented material is soft and fl...
Embodiment 2
[0021] Take 100Kg of yeast slime, add 6Kg of starch and 0.3Kg of yeast medium, stir and aerate the material to form a slurry, after 12 hours, heat up to 25°C, the number of cells under the microscope is 1.3 billion / g, and the number of living cells is more than 80%. After activation The yeast is directly used as the strain of solid fermentation.
[0022] 100Kg of soybean meal, 70Kg of bean dregs and 100Kg of beer dregs are used as fermentation raw materials, mixed with activated yeast, so that the water content is 60%, and the inoculum amount of yeast is 600 million / g. At the same time, add inorganic nutrient salts, mix and stir evenly, then stack and ferment. The nutrient salts are composed of inorganic salts containing nitrogen, phosphorus, and potassium. The amount of fermentation material is 3% ammonium sulfate, 1% urea, 0.15% calcium hydrogen phosphate, and potassium chloride. 0.05%. The thickness of the fermented materials can be piled up to 25cm. When the temperature r...
Embodiment 3
[0025] Take 100Kg of yeast slime, add 7Kg of starch and 0.2Kg of yeast medium, stir and aerate the material to form a slurry, after 11 hours, heat up to 30°C, the number of cells under the microscope is 1.5 billion / g, and the number of living cells is over 72%. After activation The yeast is directly used as the strain of solid fermentation.
[0026] 100Kg of soybean meal, 20Kg of bean dregs and 40Kg of wheat bran as auxiliary materials are used to mix with activated yeast so that the water content is 65%, and the inoculum amount of yeast is 800 million / g. At the same time, add inorganic nutrient salts, mix and stir evenly, stack and ferment. The nutrient salts are composed of inorganic salts containing nitrogen, phosphorus, and potassium. The amount of fermentation material is 2.5% ammonium sulfate, 1.5% urea, 0.15% calcium hydrogen phosphate, and potassium chloride. 0.06%. The thickness of the fermented materials can be piled up to 28cm. When the temperature rises above 45°C...
PUM
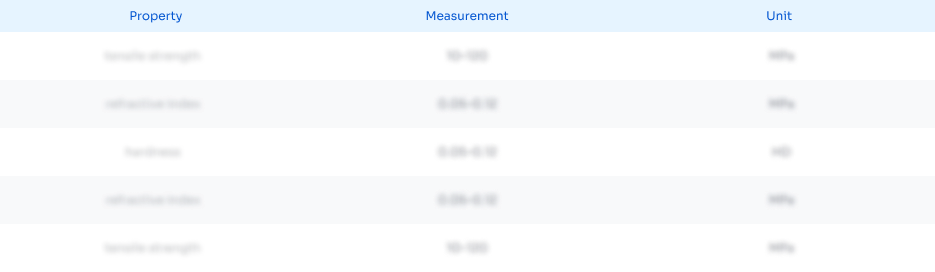
Abstract
Description
Claims
Application Information

- R&D Engineer
- R&D Manager
- IP Professional
- Industry Leading Data Capabilities
- Powerful AI technology
- Patent DNA Extraction
Browse by: Latest US Patents, China's latest patents, Technical Efficacy Thesaurus, Application Domain, Technology Topic, Popular Technical Reports.
© 2024 PatSnap. All rights reserved.Legal|Privacy policy|Modern Slavery Act Transparency Statement|Sitemap|About US| Contact US: help@patsnap.com