Hydraulic servo material tester
A material testing, hydraulic servo technology, used in measuring devices, analyzing materials, and testing material strength by applying stable tension/pressure, which can solve problems such as control instability and oscillation
- Summary
- Abstract
- Description
- Claims
- Application Information
AI Technical Summary
Problems solved by technology
Method used
Image
Examples
Embodiment Construction
[0025] Now, referring to the drawings, a description will be given of an embodiment of the present invention.
[0026] figure 1 is a schematic diagram of a device according to an embodiment of the present invention, and figure 2 It is a block diagram illustrating the detailed structure of its control system.
[0027] The test device main body 1 has a structure in which two uprights 12a and 12b are provided on a platform 11, and both ends of a transverse bracket 13 are supported by the uprights 12a and 12b.
[0028] A loading mechanism 14 is provided on the platform 11 in which a hydraulic cylinder operated by pressure oil supplied thereto through the servo valve 2 serves as an actuator. The lower jaw 15 a is fitted to this loading mechanism 14 , while the upper jaw 15 b is fitted to the aforementioned transverse support 13 via the load cell 3 . The test piece TP is used in the test in a state where both ends thereof are clamped by the upper and lower jaws 15a and 15b.
...
PUM
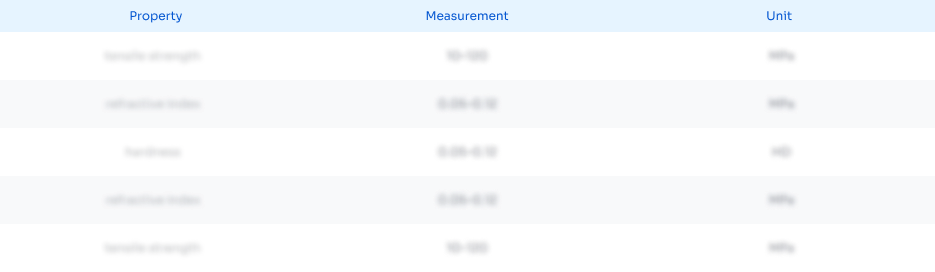
Abstract
Description
Claims
Application Information

- R&D
- Intellectual Property
- Life Sciences
- Materials
- Tech Scout
- Unparalleled Data Quality
- Higher Quality Content
- 60% Fewer Hallucinations
Browse by: Latest US Patents, China's latest patents, Technical Efficacy Thesaurus, Application Domain, Technology Topic, Popular Technical Reports.
© 2025 PatSnap. All rights reserved.Legal|Privacy policy|Modern Slavery Act Transparency Statement|Sitemap|About US| Contact US: help@patsnap.com