Handle of golf ball brassy manufacture and manufacturing device
A technology for golf balls, manufacturing devices, applied in the direction of golf balls, golf clubs, rackets, etc., capable of solving problems such as fluid outflow, lamination material curl and relaxation
- Summary
- Abstract
- Description
- Claims
- Application Information
AI Technical Summary
Problems solved by technology
Method used
Image
Examples
Embodiment Construction
[0093] Next, specific examples of the manufacturing apparatus for golf club shafts of the present invention will be described.
[0094] In this example, if Figure 5 with Image 6 As shown, the upper pressing plate 31 is formed in an overall flat plate shape, and the lower pressing plate 32 is composed of a plurality of pressing plate members 33 . Moreover, each pressing plate member 33 is formed into a rectangular prism rod shape, and the coil spring 45 is in contact with the lower portion of both ends of the pressing plate member 33, and the pressing plate member 33 contacted by the coil spring 45 is placed on the work table 41 which moves in the horizontal direction. , having a structure arranged continuously along a direction perpendicular to the rolling direction of the mandrel.
[0095] Specifically, female threaded holes 37 are provided at the lower parts of both ends of the bar-shaped pressing plate member 33 forming a quadrangular prism, and the cylindrical rod-shap...
PUM
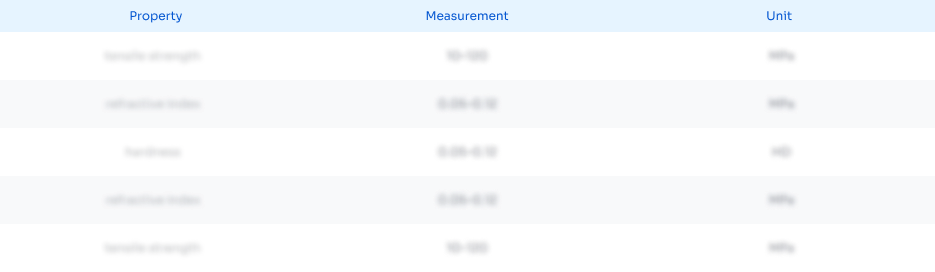
Abstract
Description
Claims
Application Information

- R&D
- Intellectual Property
- Life Sciences
- Materials
- Tech Scout
- Unparalleled Data Quality
- Higher Quality Content
- 60% Fewer Hallucinations
Browse by: Latest US Patents, China's latest patents, Technical Efficacy Thesaurus, Application Domain, Technology Topic, Popular Technical Reports.
© 2025 PatSnap. All rights reserved.Legal|Privacy policy|Modern Slavery Act Transparency Statement|Sitemap|About US| Contact US: help@patsnap.com