Process for preparing water-soluble styrenelacrylic resins by continuous bulk polymerization
A technology of bulk polymerization and styrene, applied in the field of preparing water-soluble styrene/acrylic resin by continuous bulk polymerization
- Summary
- Abstract
- Description
- Claims
- Application Information
AI Technical Summary
Problems solved by technology
Method used
Image
Examples
Embodiment I-V
[0034] Styrene monomers (styrene and α-methylstyrene) and acrylic acid monomers (acrylic acid) were charged to a continuously stirred, temperature-controlled reactor externally equipped with an oil jacket containing a cooling coil, as listed in Table 1 below. Shown to prepare water-soluble styrene / acrylic resin.
[0035] Polymerization was initiated in the presence of t-butylperoxybenzoate. The polymerization initiator is used in an amount of 3.5 parts by weight, based on the total weight of the monomer mixture. For the polymerization, 15 parts by weight of a mixed solvent of dipropylene glycol methyl ether and water having a water content of 35% by weight were used, based on 100 parts by weight of the monomer mixture. Polymerization was carried out under different temperature conditions ranging from 150 to 220°C. The polymerized resin passes through the falling strand type exhaust section, from which the volatile components are removed. At the same time, the exhaust sectio...
Embodiment VI-IX
[0043] In order to investigate the effect of the operating conditions of the vent section on the physical properties of the resin, the polymerization was carried out in the same manner as in Example IV, but under the temperature and pressure conditions of the vent section shown in Table 3 below. The results are shown in Table 3.
[0044] Example number
Embodiment X-XIII
[0050] A water-soluble styrene / acrylic resin was prepared in a manner similar to Example IV, except that the amount and water content of the mixed solvent of dipropylene glycol methyl ether and water were changed, as shown in Table 5 below.
PUM
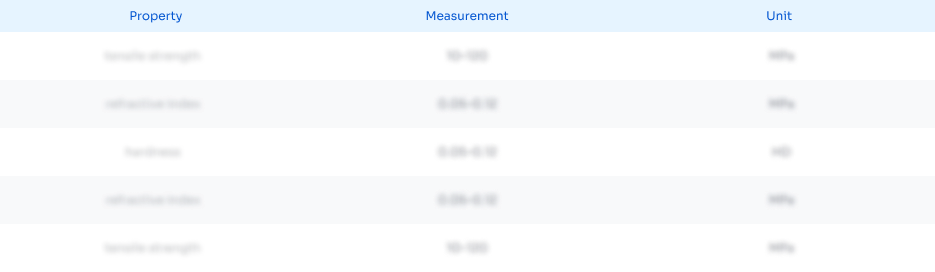
Abstract
Description
Claims
Application Information

- Generate Ideas
- Intellectual Property
- Life Sciences
- Materials
- Tech Scout
- Unparalleled Data Quality
- Higher Quality Content
- 60% Fewer Hallucinations
Browse by: Latest US Patents, China's latest patents, Technical Efficacy Thesaurus, Application Domain, Technology Topic, Popular Technical Reports.
© 2025 PatSnap. All rights reserved.Legal|Privacy policy|Modern Slavery Act Transparency Statement|Sitemap|About US| Contact US: help@patsnap.com