Planetary gear device and driving component with same
A technology of planetary gears and planetary gear racks, applied to components with teeth, gear transmissions, transmission parts, etc., can solve problems such as large structural space and achieve the effect of simple structure
- Summary
- Abstract
- Description
- Claims
- Application Information
AI Technical Summary
Problems solved by technology
Method used
Image
Examples
Embodiment Construction
[0018] A sun gear coaxial with the main axis 4 of the transmission is denoted by 2 in FIG. 1 . The sun gear 2 is fixedly connected in rotation with the sun gear shaft 6, and the sun gear shaft has a mounting area 8, which is used for a motor not shown in the figure that can be mounted on the motor flange 10 through a flange. motor shaft. The housing of the planetary gear unit consists of two housing parts 12A, 12B. A hollow gear 14 is machined in the housing part 12B. A plurality of planet gears 16 (only one of which is shown) are rotatably supported on planet gear pins 18 via planet gear bearings 20 . The planet pins 18 or the planet gears 16 are arranged distributed over the circumference of the planet carrier 22 and mesh simultaneously with the sun gear 2 and the hollow gear 10 . The planet carrier 22 forms the driven device and is designed in one piece with the output shaft 24 . However, the planet carrier and the output shaft can also be connected via a rotationally f...
PUM
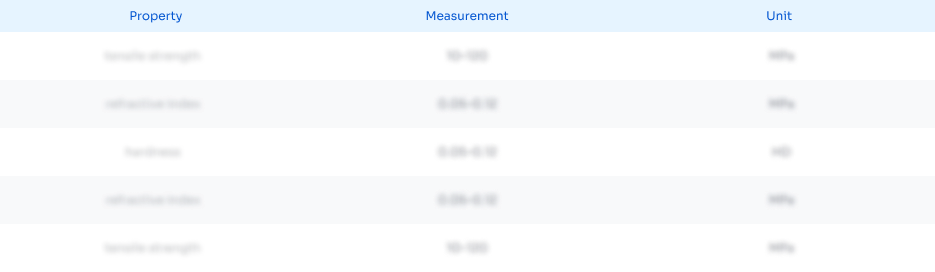
Abstract
Description
Claims
Application Information

- Generate Ideas
- Intellectual Property
- Life Sciences
- Materials
- Tech Scout
- Unparalleled Data Quality
- Higher Quality Content
- 60% Fewer Hallucinations
Browse by: Latest US Patents, China's latest patents, Technical Efficacy Thesaurus, Application Domain, Technology Topic, Popular Technical Reports.
© 2025 PatSnap. All rights reserved.Legal|Privacy policy|Modern Slavery Act Transparency Statement|Sitemap|About US| Contact US: help@patsnap.com