Active control method for output feedback dynamic surface based on flutter of micro-milling processing system
A processing system and output feedback technology, applied in the field of active control of output feedback dynamic surface based on micro-milling processing system chatter, can solve problems such as observer error and failure, and achieve the effect of reducing computational burden and simple control law
- Summary
- Abstract
- Description
- Claims
- Application Information
AI Technical Summary
Problems solved by technology
Method used
Image
Examples
Embodiment 1
[0057] An output feedback dynamic surface active control method based on the chatter vibration of a micro-milling machining system, comprising the following steps:
[0058] (1) Establish a dynamic model for the chatter of the cutter head of the micro-milling machining system;
[0059] like figure 1 As shown, the micro-milling machining system is approximated as a two-degree-of-freedom system. The cutting force model of micro-milling can be expressed as
[0060]
[0061] Among them, F X , F Y are the cutting forces in the X and Y directions, F tn , F rn Tangential and radial cutting forces for the nth tooth, K t and K r respectively represent the tangential cutting force coefficient and the radial cutting force coefficient, C t and C r respectively represent the tangential damping force coefficient and the radial damping force coefficient, V c is the cutting speed, N represents the number of teeth of the micro-milling cutter, φ n represents the intrusion angle of ...
PUM
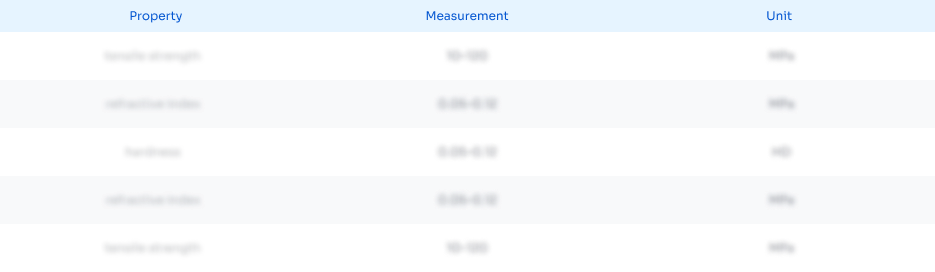
Abstract
Description
Claims
Application Information

- R&D
- Intellectual Property
- Life Sciences
- Materials
- Tech Scout
- Unparalleled Data Quality
- Higher Quality Content
- 60% Fewer Hallucinations
Browse by: Latest US Patents, China's latest patents, Technical Efficacy Thesaurus, Application Domain, Technology Topic, Popular Technical Reports.
© 2025 PatSnap. All rights reserved.Legal|Privacy policy|Modern Slavery Act Transparency Statement|Sitemap|About US| Contact US: help@patsnap.com