Adaptive output feedback inverse control method for piezoelectric precision position platform
An output feedback and self-adaptive technology, which is applied in the field of precision machining and manufacturing, can solve the problems that it is difficult to obtain the output feedback control scheme of the hysteresis inverse compensator, invalid, unobtainable, etc.
- Summary
- Abstract
- Description
- Claims
- Application Information
AI Technical Summary
Problems solved by technology
Method used
Image
Examples
Embodiment Construction
[0142] The present invention will be further described below using the accompanying drawings and examples.
[0143] The adaptive output feedback inverse control method of the piezoelectric precision position platform of the present invention includes the following contents:
[0144] 1) Mathematical model of piezoelectric precision position platform
[0145] Considering a class of nonlinear system with hysteresis added:
[0146]
[0147]
[0148] y=x 1 ,i=0,1,...,n-1 (1)
[0149] in, is the state vector; Unknown smooth linear function, d i (t) is the external disturbance, b 0 The unknown constant parameter, w∈R unknown hysteresis, is expressed as:
[0150] w(u)=P(u(t)) (2)
[0151] u is the input signal of the actuator, P is the lag operator,
[0152] For the system (1), the following assumptions are necessary:
[0153] A1: interference d i (t), i=1,···,n, satisfy:
[0154]
[0155] in, are some unknown normal constants; A2: Under the design process, th...
PUM
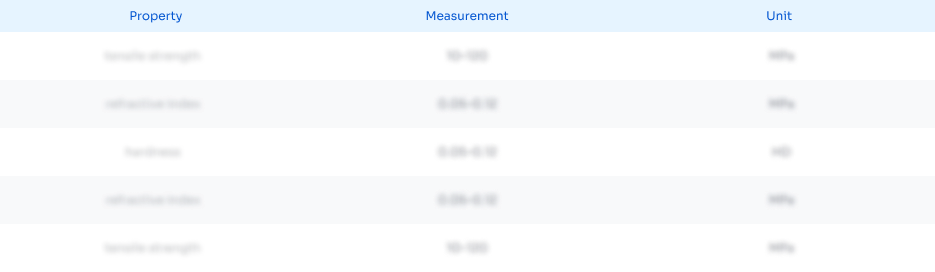
Abstract
Description
Claims
Application Information

- Generate Ideas
- Intellectual Property
- Life Sciences
- Materials
- Tech Scout
- Unparalleled Data Quality
- Higher Quality Content
- 60% Fewer Hallucinations
Browse by: Latest US Patents, China's latest patents, Technical Efficacy Thesaurus, Application Domain, Technology Topic, Popular Technical Reports.
© 2025 PatSnap. All rights reserved.Legal|Privacy policy|Modern Slavery Act Transparency Statement|Sitemap|About US| Contact US: help@patsnap.com