3D concrete printing path planning method for realizing inclined top surface
A printing path and 3D printing technology, applied in geometric CAD, instruments, manufacturing tools, etc., can solve the problems of drastic changes in the position of the printing line, separation, and overhanging the upper and lower printing materials, so as to improve accuracy and stability. Solve material accumulation and reduce the effect of complicated processes
- Summary
- Abstract
- Description
- Claims
- Application Information
AI Technical Summary
Problems solved by technology
Method used
Image
Examples
Embodiment 1
[0077] Example 1: Illustration of a case of adding a mezzanine between adjacent variable planes
[0078] see attached figure 2 , this embodiment is a cylindrical concrete flowerpot with a sloped top, its model structure is relatively simple, and the ratio of the highest point elevation to the lowest point elevation on the top surface is 2:1, so a sandwich can be added between adjacent variable planes To achieve the printing path generation of the flowerpot, figure 2 a- figure 2e shows the layering process of the flower pot model. The steps of generating the path can be implemented according to the above-described process, wherein a takes the value of 2, and k takes the value of 1.
[0079] figure 2 a shows the overall shape of the first embodiment, figure 2 b shows the top and bottom planes of the extracted 3D model, figure 2 c shows a whole-layer variable-planar slice that generates a uniform change between the top and bottom planes, figure 2 d shows the inserti...
Embodiment 2
[0080] Example 2: Illustration of a case where two interlayers are added between adjacent variable planes
[0081] see attached image 3 , the slope of this embodiment is gentle, but the overall height of the model is very low, so the ratio of the highest point to the lowest point at the top still reaches 3:1. In addition, the text part of the topmost surface of the model is a separate protruding structure, Therefore, in this embodiment, the top surface of the pattern portion is considered as the top surface of the variable plane slice, see image 3 b, and the text part is sliced with a plane parallel to the top surface of the pattern, see image 3 e shown. That is to say, a step needs to be added between steps 8 and 9, and the top plane of the pattern part is translated n times up along the Z-axis direction, n=int(H top / m), the distance is H top / n, where H top is the height of the text protruding in the Z-axis direction, m is the plane offset distance calculated in s...
Embodiment 3
[0083] Example 3: Example of adding three interlayers between adjacent variable planes
[0084] see attached Figure 4 , the characteristics of this embodiment are that the slope of the top surface is relatively large, the ratio of the elevation of the highest point to the lowest point reaches 4:1, and the side of the body is an arc. The way the model is cut does not evenly divide the sides of this arc. Therefore, in this embodiment, it is not only necessary to add three sets of interlayers between the whole layer and the plane, but also to change the way of defining the segmentation range in step 6 . Specifically, step 6 will be adjusted to: retain the method of determining the slicing line in step 6-1, but in step 6-2, instead of using the Z-axis direction to cut the model, let each slicing line Sweep along the trajectory of the arc on the side of the model to cut the model, such as Figure 4 As shown in d, this segmentation method can ensure that the planes within each t...
PUM
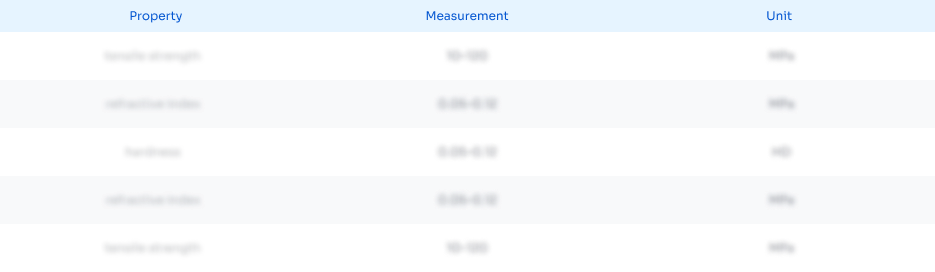
Abstract
Description
Claims
Application Information

- Generate Ideas
- Intellectual Property
- Life Sciences
- Materials
- Tech Scout
- Unparalleled Data Quality
- Higher Quality Content
- 60% Fewer Hallucinations
Browse by: Latest US Patents, China's latest patents, Technical Efficacy Thesaurus, Application Domain, Technology Topic, Popular Technical Reports.
© 2025 PatSnap. All rights reserved.Legal|Privacy policy|Modern Slavery Act Transparency Statement|Sitemap|About US| Contact US: help@patsnap.com