Forming method of thin web forge piece
A thin web and forging technology is applied in the forming field of thin web forgings. The effect of shortening the production cycle
- Summary
- Abstract
- Description
- Claims
- Application Information
AI Technical Summary
Problems solved by technology
Method used
Image
Examples
Embodiment Construction
[0030] The present invention will be further described below in conjunction with the accompanying drawings and embodiments.
[0031] like Figure 1 to Figure 8 As shown, in the method for forming a thin web forging according to the present invention, the forging 8 includes a base plate 81, a rib structure A arranged on one side of the base plate 81 and a rib structure B arranged on the other side of the base plate 81. The forming method includes the following steps:
[0032] Step 1, blank making: according to the length of the base plate 81, the rod 1 is elongated to obtain a cylindrical blank 2, and the length of the blank blank 2 is basically the same as the length of the base plate 81;
[0033] Step 2, pre-forging: configure a pre-forging die, the pre-forging die includes a pre-forging die upper die 4 and a pre-forging die lower die 3, and the lower surface of the pre-forging die upper die 4 is provided with a structural design according to the base plate 81. The pre-forg...
PUM
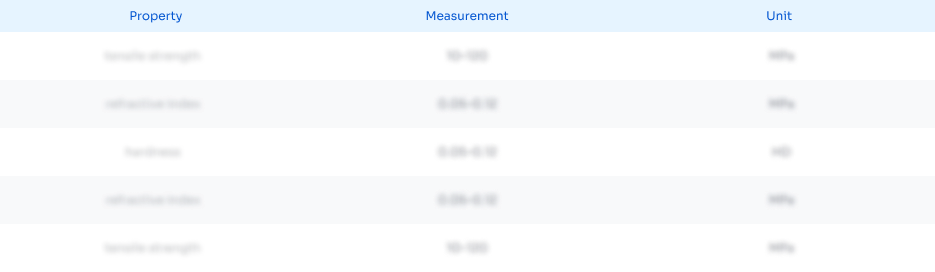
Abstract
Description
Claims
Application Information

- Generate Ideas
- Intellectual Property
- Life Sciences
- Materials
- Tech Scout
- Unparalleled Data Quality
- Higher Quality Content
- 60% Fewer Hallucinations
Browse by: Latest US Patents, China's latest patents, Technical Efficacy Thesaurus, Application Domain, Technology Topic, Popular Technical Reports.
© 2025 PatSnap. All rights reserved.Legal|Privacy policy|Modern Slavery Act Transparency Statement|Sitemap|About US| Contact US: help@patsnap.com