Static load loading system and method in high-temperature thermal strength test for aerospace plane test
A technology for aerospace aircraft and strength testing, which is applied in the direction of aircraft component testing, machine/structural component testing, and measuring devices. It can solve problems affecting the accuracy of aircraft high-temperature thermal strength testing, and achieve test and research work promotion and connection stability. The effect of high and reliable equipment support
- Summary
- Abstract
- Description
- Claims
- Application Information
AI Technical Summary
Problems solved by technology
Method used
Image
Examples
Embodiment 1
[0041] like figure 2 , 3 , The static load loading system in the high temperature thermal strength test for aerospace aircraft testing shown in 4 and 5 includes a bracket 1, an actuator 2 movably clamped on the bracket 1 and a static load threaded on the actuator 2. The loading assembly 3; the bracket 1 includes a base 10, four support rods 11 movably clamped on the base 10, and a limit plate 12 arranged above the base 10 and fixedly connected to the upper ends of the support rods 11 respectively; the base 10 is horizontal An adjustment slot 100 is provided, and an adjustment screw 101 is rotated and clamped inside the adjustment slot 100. The upper end surface of the base 10 is provided with a micro motor 102 that provides power for the adjustment screw 101; the limit plate 12 is provided with a strip-shaped through slot 120;
[0042] like figure 2 , 4 , 6, the bottom end of the actuator 2 is slidably connected with a compensation sleeve 20, and the bottom end of the com...
Embodiment 2
[0045] What this embodiment records is the loading method of the static load loading system in the high-temperature thermal strength test for the aerospace aircraft test of Embodiment 1, comprising the following steps:
[0046] S1. Connect the micromotor 102 and the actuator 2 to an external power supply respectively;
[0047] S2. According to the loading requirements of the static load in the high temperature thermal strength test of the aerospace aircraft, adjust the load loading angle of the actuator 2, then turn on the micro motor 102, and use the micro motor 102 to drive the adjustment screw 101 to rotate, so that the thread moves the seat 21 moves in the adjustment groove 100, at this time the bottom end of the actuator 2 moves with the thread moving seat 21 under the action of the compensation sleeve 20, and the top end of the actuator 2 swings in the bar-shaped through groove 120 on the limit plate 12;
[0048] S3. After the adjustment of the load loading angle of the ...
Embodiment 3
[0051] This embodiment differs from Embodiment 1 in that:
[0052] like figure 2 , 5 As shown in the figure, the upper end face of the base 10 is rotatably connected with a rotating disk 13, and the adjusting screw 101 and the micro motor 102 are both arranged on the rotating disk 13. The upper end surface of the base 10 and the outer side of the rotating disk 13 are provided with annular clamping grooves 14, each supporting The bottom ends of the rods 11 are all rotatably clamped with rotating rollers 110 that are movably clamped with the annular clamping grooves 14;
[0053] A fixing plate 15 is sleeved on the outer wall of the base 10 , and six mounting holes 150 are provided through the fixing plate 15 .
PUM
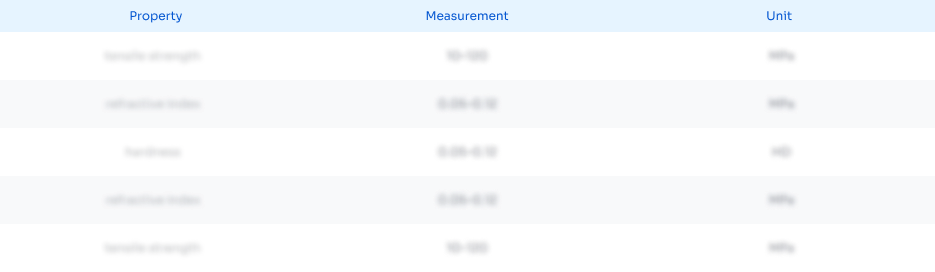
Abstract
Description
Claims
Application Information

- R&D
- Intellectual Property
- Life Sciences
- Materials
- Tech Scout
- Unparalleled Data Quality
- Higher Quality Content
- 60% Fewer Hallucinations
Browse by: Latest US Patents, China's latest patents, Technical Efficacy Thesaurus, Application Domain, Technology Topic, Popular Technical Reports.
© 2025 PatSnap. All rights reserved.Legal|Privacy policy|Modern Slavery Act Transparency Statement|Sitemap|About US| Contact US: help@patsnap.com