Turbine guide blade welding positioning method
A turbine guide vane, welding positioning technology, applied in welding equipment, auxiliary welding equipment, welding/cutting auxiliary equipment, etc., can solve the problem of large error of turbine blades
- Summary
- Abstract
- Description
- Claims
- Application Information
AI Technical Summary
Problems solved by technology
Method used
Image
Examples
specific Embodiment approach
[0058] As a specific implementation manner, a group of high-pressure turbine guide vanes that are welded by a certain two vanes are selected for description below, and the positioning before welding is performed according to the following method.
[0059] 1. Calculate the theoretical value
[0060] The Cartesian coordinate system that defines the theoretical blade is (X, Y, Z), the X axis is the engine axis, and the Z axis is the radial direction of the blade. The radius r of the cylindrical tangent surface is the distance from the origin O to the projected point M' of the point M on the plane YOZ, r∈[0,∞).
[0061] According to the blade profile distribution in the radial direction, three groups of r values are determined, which are numbered from 1 to 3 from the blade tip to the blade root, and r 1 =340mm, r 2 =330mm, r 3 =320mm.
[0062] respectively use r 1 , r 2 , r 3 The blade is cut from the cylindrical section at the maximum value, and three sets of intersectio...
PUM
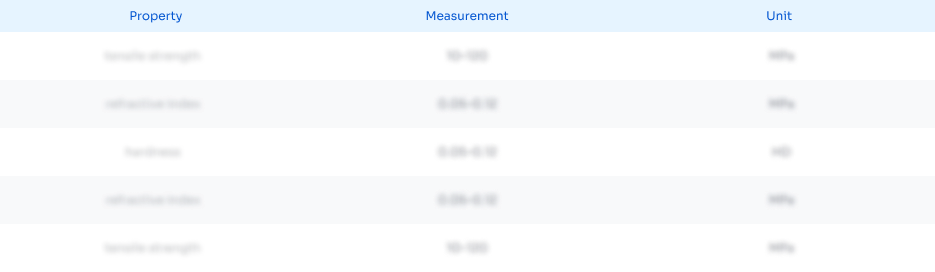
Abstract
Description
Claims
Application Information

- R&D
- Intellectual Property
- Life Sciences
- Materials
- Tech Scout
- Unparalleled Data Quality
- Higher Quality Content
- 60% Fewer Hallucinations
Browse by: Latest US Patents, China's latest patents, Technical Efficacy Thesaurus, Application Domain, Technology Topic, Popular Technical Reports.
© 2025 PatSnap. All rights reserved.Legal|Privacy policy|Modern Slavery Act Transparency Statement|Sitemap|About US| Contact US: help@patsnap.com