Error verification method of CA oscillating structure five-axis machine tool
A calibration method and error technology, applied in computer control, metal processing machinery parts, measuring/indicating equipment, etc., can solve problems such as long test period, complicated operation, and high cost
- Summary
- Abstract
- Description
- Claims
- Application Information
AI Technical Summary
Problems solved by technology
Method used
Image
Examples
Embodiment Construction
[0035] The present invention will be further described in detail below in conjunction with the accompanying drawings and embodiments.
[0036] 1. Error-free kinematics model
[0037] The structure of the error-free CA swing head five-axis machine tool is attached figure 2 As shown, this type of machine tool has two rotary axes, C-axis and A-axis, which rotate around the Z-axis linear axis and the X-axis linear axis respectively.
[0038]Among them, is the offset vector from the C-axis rotation center to the A-axis rotation center, is the offset vector from the A-axis rotation center to the spindle rotation center, and is the actual tool length.
[0039] According to the structure of the CA swing head machine tool, using the homogeneous coordinate transformation and the kinematic modeling theory of the five-axis machine tool, the following kinematic model is established:
[0040] Among them, Rot is the rotation matrix, Trans is the translation matrix, (Q x , Q y , Q z ) r...
PUM
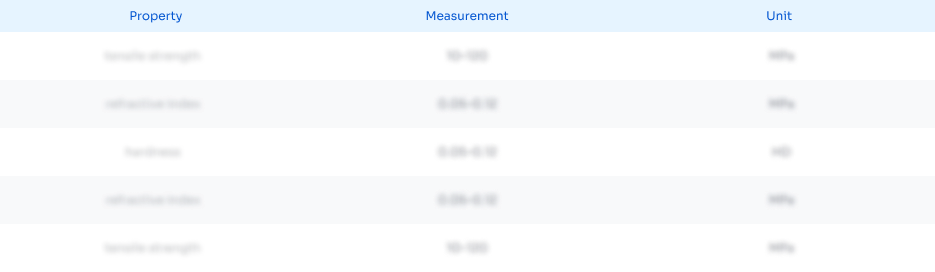
Abstract
Description
Claims
Application Information

- R&D
- Intellectual Property
- Life Sciences
- Materials
- Tech Scout
- Unparalleled Data Quality
- Higher Quality Content
- 60% Fewer Hallucinations
Browse by: Latest US Patents, China's latest patents, Technical Efficacy Thesaurus, Application Domain, Technology Topic, Popular Technical Reports.
© 2025 PatSnap. All rights reserved.Legal|Privacy policy|Modern Slavery Act Transparency Statement|Sitemap|About US| Contact US: help@patsnap.com