Chemical mechanical polishing pad and preparation method thereof
A chemical-mechanical and polishing pad technology, applied in the field of polishing pads, can solve the problems of decreased elasticity of the polishing cloth, not satisfying the polishing pad at the same time, and damage to the followability.
- Summary
- Abstract
- Description
- Claims
- Application Information
AI Technical Summary
Problems solved by technology
Method used
Image
Examples
preparation example Construction
[0036] The invention provides a preparation method of a chemical mechanical polishing pad, and the preparation method comprises the following steps:
[0037] Step 1: stirring and mixing the materials, vacuuming and defoaming after mixing to prepare resin slurry;
[0038] Step 2: The film-forming substrate is coated with a release agent, and the resin slurry is blade-coated on the film-forming substrate
[0039] Step 3: The film-forming substrate is coagulated for the first time, and the coagulation time is 0.5-5 minutes to obtain a peelable semi-cured resin slurry, and the semi-cured resin slurry is removed from the film-forming substrate. peel off;
[0040] Step 4: performing a second coagulation on the semi-cured resin slurry peeled from the film-forming substrate, the coagulation time is more than 10 minutes, and a polishing pad is obtained after processing;
[0041] The vacuum deaeration is completed by a vacuum deaeration mixer, which is a stirring and mixing equipment ...
Embodiment 1
[0071] Example 1: as figure 2 As shown, a preparation method of a two-stage condensed film-forming polishing pad is provided, and the preparation method comprises:
[0072] Step 1: stirring and mixing the materials, vacuuming and defoaming after mixing to prepare resin slurry 51;
[0073] Step 2: The film-forming substrate 41 is coated with a release agent, and the resin slurry is blade-coated on the film-forming substrate
[0074] Step 3: The film-forming substrate enters the coagulation liquid 21, and the first coagulation is performed. The coagulation time is 1.5 minutes to obtain a peelable semi-cured resin slurry, and the semi-cured resin slurry is removed from the The film substrate is peeled off, and the peeling occurs in the coagulation liquid 22;
[0075] Step 4: The resin slurry in the semi-cured state peeled off on the film-forming substrate is coagulated for the second time in the coagulation liquid 22, and the coagulation time is 15 minutes, and a polishing pad...
Embodiment 2
[0076] Example 2: as figure 2 As shown, a preparation method of a two-stage condensed film-forming polishing pad is provided, and the preparation method comprises:
[0077] Step 1: stirring and mixing the materials, vacuuming and defoaming after mixing to prepare resin slurry 51;
[0078] Step 2: The film-forming substrate 41 is coated with a release agent, and the resin slurry is blade-coated on the film-forming substrate
[0079]Step 3: The film-forming substrate enters the coagulation liquid 21, and the first coagulation is performed. The coagulation time is 1.5 minutes to obtain a peelable semi-cured resin slurry, and the semi-cured resin slurry is removed from the The film substrate is peeled off, and the peeling occurs in the coagulation liquid 22;
[0080] Step 4: The resin slurry in the semi-cured state peeled off on the film-forming substrate is coagulated for the second time in the coagulation liquid 22, and the coagulation time is 15 minutes, and a polishing pad ...
PUM
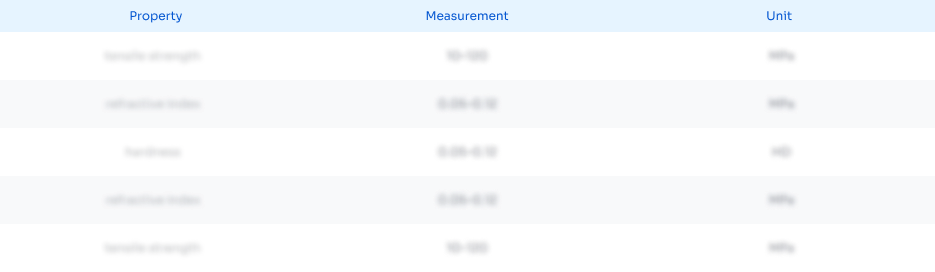
Abstract
Description
Claims
Application Information

- Generate Ideas
- Intellectual Property
- Life Sciences
- Materials
- Tech Scout
- Unparalleled Data Quality
- Higher Quality Content
- 60% Fewer Hallucinations
Browse by: Latest US Patents, China's latest patents, Technical Efficacy Thesaurus, Application Domain, Technology Topic, Popular Technical Reports.
© 2025 PatSnap. All rights reserved.Legal|Privacy policy|Modern Slavery Act Transparency Statement|Sitemap|About US| Contact US: help@patsnap.com