Real-time monitoring method and system for falling, sucking and mounting of elements in chip mounter
A real-time monitoring and placement machine technology, which is applied in the direction of assembling printed circuits, electrical components, electrical components, etc., can solve the problem that it is difficult to effectively monitor the suction and placement status of components, and the suction vacuum pressure has a small range of changes , Affecting the quality of component placement and other issues, to achieve the effect of improving the success rate of absorption, simple calculation method, and improving reliability
- Summary
- Abstract
- Description
- Claims
- Application Information
AI Technical Summary
Problems solved by technology
Method used
Image
Examples
Embodiment 1
[0072] A real-time monitoring method for component drop, such as figure 2 shown, including the following steps:
[0073] S11: The initialization vacuum pressure sampling rate is 12500Hz (sampling interval is 80μs), and the storage vacuum pressure array queue length is 100, then the queue length is 100*80μs=8ms and the component drop monitoring threshold (denoted as Threshold);
[0074] S12: as figure 2 As shown, when the nozzle rod of the placement head is in the suction state, the collected vacuum pressure data is stored in the array queue. When the array queue is not full, add the vacuum pressure data to the end of the previous one; when the array queue is full, collect 1 vacuum pressure data -70.3 and add it to the end of the array queue, and delete 1 data at the head of the array queue point-88.1;
[0075] S13: Determine whether the array queue is full of storage, if not, enter the step S12, if the storage is full, calculate the vacuum pressure change rate. According...
Embodiment 2
[0082] A real-time monitoring method for component pickup, such as Figure 4 shown, including the following steps:
[0083] S21: Initialization parameters, including vacuum pressure sampling rate of 12500Hz (sampling interval of 80μs), storage vacuum pressure array queue length of 100, queue length of 100*80μs=8ms, suction height of 0mm, suction timing of 50ms, vacuum pressure The difference threshold is 1.0kPa;
[0084] S22: The nozzle rod of the placement head is opened to inhale in advance and the nozzle rod is lowered;
[0085] S23: During the descending process of the nozzle rod, the sampled vacuum pressure data is stored in the array queue. When the array queue is not full, the vacuum pressure data is appended to the end of the previous one; when the array queue is full, one vacuum pressure data is collected. Data is added to the end of the array queue, and 1 data point at the head of the array sequence is deleted;
[0086] S24: When the nozzle rod descends to the "su...
Embodiment 3
[0089] A real-time monitoring method for mounted components, the realization flow chart is as follows Figure 5 shown, including the following steps:
[0090] S31: Initialize the "mounting height" and "mounting timing" parameters;
[0091] S32: After the nozzle rod descends until it reaches the "mounting height", the nozzle rod stops moving;
[0092] S33: execute the blowing action in parallel, start the "placement timing" timer and monitor the vacuum pressure;
[0093] S34: Real-time monitoring of vacuum pressure data and "mounting timing" timer, when it is detected that the vacuum pressure data is positive pressure, that is, when the value is greater than 0, it is considered that the component has been mounted, and the gas stop and nozzle rod are executed in parallel Rising action; when it is detected that the vacuum pressure is negative pressure, wait. When the "Place Timing" timer is triggered, the air stop and nozzle rod ascending actions are performed in parallel.
...
PUM
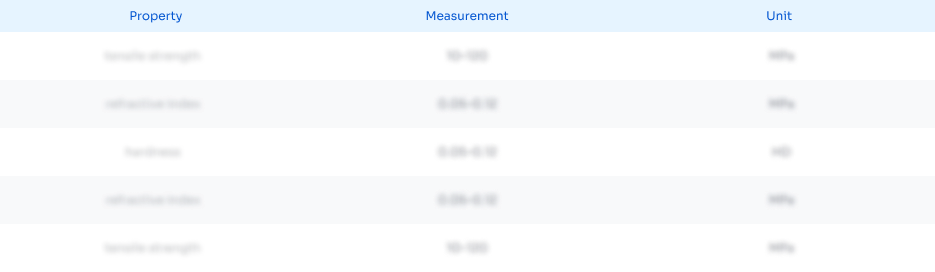
Abstract
Description
Claims
Application Information

- R&D
- Intellectual Property
- Life Sciences
- Materials
- Tech Scout
- Unparalleled Data Quality
- Higher Quality Content
- 60% Fewer Hallucinations
Browse by: Latest US Patents, China's latest patents, Technical Efficacy Thesaurus, Application Domain, Technology Topic, Popular Technical Reports.
© 2025 PatSnap. All rights reserved.Legal|Privacy policy|Modern Slavery Act Transparency Statement|Sitemap|About US| Contact US: help@patsnap.com