Sheet falling prevention manufacturing method of conductive foam die cutting piece
A technology of conductive foam and production method, which is applied in the field of die-cutting parts processing, can solve the problems of time-consuming, labor-consuming, manpower, chipping and displacement of adjusting the machine, saving labor-hours, improving production efficiency, and reducing materials The effect of loss
- Summary
- Abstract
- Description
- Claims
- Application Information
AI Technical Summary
Problems solved by technology
Method used
Image
Examples
Embodiment
[0040] A method for producing an anti-drop sheet of a conductive foam die-cut piece, such as figure 1 and 8 , conductive foam including polyurethane sponge, conductive cloth and conductive glue, such as Figure 9 , the method includes the following steps:
[0041] (1) Lamination of the first-level material tape: the release film 12 is attached to the protective film 11 to form a first-level material belt;
[0042] (2) One punch die cutting: such as Figure 2-3 , the first-grade material is cut in a die-cutting machine; a die-cutting machine is provided with a knife line a matching the pattern of a die-cut, and the punching layer of the knife line a is the release film 12 . The cutter line a is at an angle of 30° with the running direction of the material belt.
[0043] (3) Lamination of the secondary material tape: the conductive foam 21 is bonded on the release film 12 to form a secondary material tape;
[0044] (4) Two-punch die-cutting waste disposal: such as Figure ...
PUM
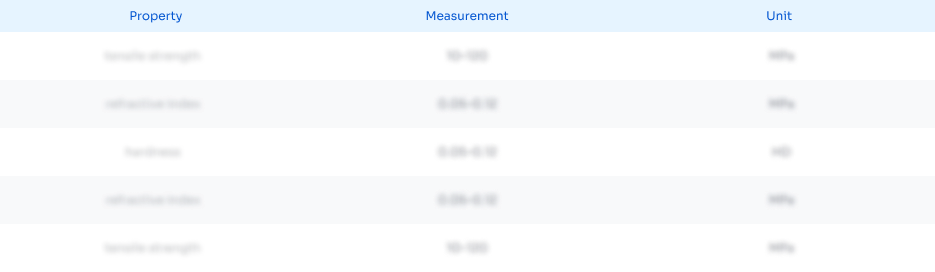
Abstract
Description
Claims
Application Information

- R&D
- Intellectual Property
- Life Sciences
- Materials
- Tech Scout
- Unparalleled Data Quality
- Higher Quality Content
- 60% Fewer Hallucinations
Browse by: Latest US Patents, China's latest patents, Technical Efficacy Thesaurus, Application Domain, Technology Topic, Popular Technical Reports.
© 2025 PatSnap. All rights reserved.Legal|Privacy policy|Modern Slavery Act Transparency Statement|Sitemap|About US| Contact US: help@patsnap.com