Rapid calibration method for visual sensor
A visual sensor and calibration method technology, applied in the field of calibration, can solve the problems of low efficiency, complicated operation, and difficulty in ensuring accuracy, and achieve the effects of ensuring accuracy, improving calibration efficiency, and saving calibration time.
- Summary
- Abstract
- Description
- Claims
- Application Information
AI Technical Summary
Problems solved by technology
Method used
Image
Examples
Embodiment Construction
[0055] The present invention is further described in detail below:
[0056] A visual sensor rapid calibration method provided by the present invention includes the following steps: S1. Set the camera at the end of the robot tool hand, and determine the relative pose matrix T of the camera relative to the end of the robot tool hand;
[0057] S2. set up a calibration board, the calibration board is provided with a checkerboard and AprilTags code, the camera obtains the AprilTags code and determines the center position Pa of the AprilTags code, and calculates the center position Pc of the checkerboard according to the center position Pa of the AprilTags code ; Wherein, the central position Pc of the checkerboard is calculated with the central position Pa of the AprilTags code and is realized by the existing geometric algorithm;
[0058] S3. Control the camera to face the checkerboard center position Pc, and then control the robot tool hand to change the posture to collect the che...
PUM
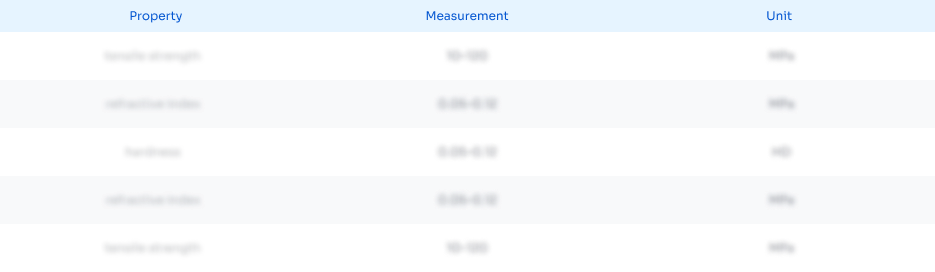
Abstract
Description
Claims
Application Information

- R&D Engineer
- R&D Manager
- IP Professional
- Industry Leading Data Capabilities
- Powerful AI technology
- Patent DNA Extraction
Browse by: Latest US Patents, China's latest patents, Technical Efficacy Thesaurus, Application Domain, Technology Topic, Popular Technical Reports.
© 2024 PatSnap. All rights reserved.Legal|Privacy policy|Modern Slavery Act Transparency Statement|Sitemap|About US| Contact US: help@patsnap.com