LED backlight module preparation method and LED backlight module
A technology of backlight modules and LED chips, which is applied to identification devices, instruments, semiconductor devices, etc., and can solve the problems of large overall thickness and high cost of LED backlight modules
- Summary
- Abstract
- Description
- Claims
- Application Information
AI Technical Summary
Problems solved by technology
Method used
Image
Examples
preparation example Construction
[0044] The embodiment of the present invention provides a method for preparing an LED backlight module, see figure 1 As shown, it includes the steps:
[0045] S101: setting several LED chips on the front surface of the substrate.
[0046] In this step, each LED chip is fixed on the front surface of the substrate, and each LED chip is evenly distributed on the front surface of the substrate according to a preset array layout.
[0047] S102: Making an encapsulation adhesive layer for sealing a plurality of LED chips.
[0048]The encapsulation adhesive layer is used for sealing and protecting the LED chips arranged on the front surface of the substrate.
[0049] S103: Using pre-made optical glue, arranging several light diffusion units at intervals on the light-emitting surface of the encapsulation glue layer.
[0050] Before this step, it also includes mixing the light diffusion particles into the glue solvent according to a predetermined ratio to prepare optical glue. This s...
PUM
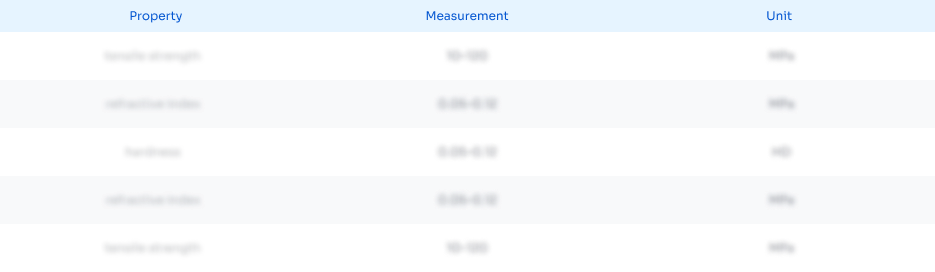
Abstract
Description
Claims
Application Information

- R&D Engineer
- R&D Manager
- IP Professional
- Industry Leading Data Capabilities
- Powerful AI technology
- Patent DNA Extraction
Browse by: Latest US Patents, China's latest patents, Technical Efficacy Thesaurus, Application Domain, Technology Topic, Popular Technical Reports.
© 2024 PatSnap. All rights reserved.Legal|Privacy policy|Modern Slavery Act Transparency Statement|Sitemap|About US| Contact US: help@patsnap.com