Multi-point discrete precise straightening planning method for planar curved linear guide rail
A linear guide rail and plane bending technology, which is applied in the direction of comprehensive factory control and complex mathematical operations, can solve the problems of single-step straightening limitations, and achieve the effect of improving straightening processing efficiency and straight line accuracy of linear guide rails
- Summary
- Abstract
- Description
- Claims
- Application Information
AI Technical Summary
Problems solved by technology
Method used
Image
Examples
Embodiment Construction
[0073] The present invention will be described in detail below with reference to the accompanying drawings and embodiments.
[0074] refer to figure 1 As shown, the multi-point discrete precision straightening planning method for a plane curved linear guide rail in an embodiment provided by the present invention includes the following steps:
[0075] 1) Establish a comprehensive coordinate system for the multi-point discrete precision straightening process of the plane curved linear guide, and the comprehensive coordinate system for describing the multi-point discrete precision straightening process includes the workpiece measurement coordinate system {S M }, Workpiece reference coordinate system {S W }, workpiece straightening coordinate system {S S } and the local coordinate system of the straightening indenter {S T };
[0076] 2) The workpiece measurement coordinate system {S M } The linear guide plane deflection curve expression is converted into the workpiece referen...
PUM
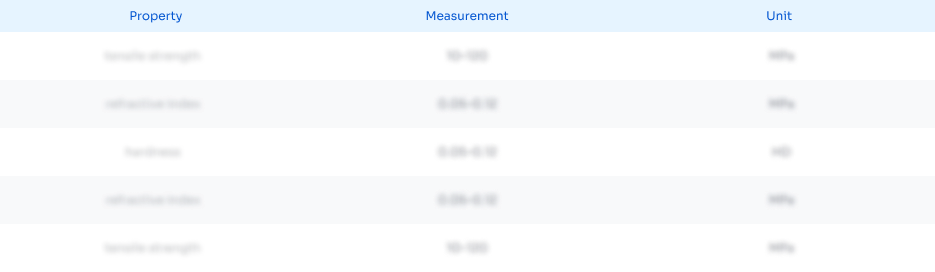
Abstract
Description
Claims
Application Information

- Generate Ideas
- Intellectual Property
- Life Sciences
- Materials
- Tech Scout
- Unparalleled Data Quality
- Higher Quality Content
- 60% Fewer Hallucinations
Browse by: Latest US Patents, China's latest patents, Technical Efficacy Thesaurus, Application Domain, Technology Topic, Popular Technical Reports.
© 2025 PatSnap. All rights reserved.Legal|Privacy policy|Modern Slavery Act Transparency Statement|Sitemap|About US| Contact US: help@patsnap.com