Simple complex cavity blade core pulling method based on UG modeling
A complex, bladed technology, applied in the field of simple core pulling of complex cavity blades, can solve the problems of structure prone to error, error prone, entity excess, etc., and achieve the effect of simplifying the filling process, less error-prone and improving efficiency.
- Summary
- Abstract
- Description
- Claims
- Application Information
AI Technical Summary
Problems solved by technology
Method used
Image
Examples
Embodiment Construction
[0017] In order to make the technical means, creative features, goals and effects achieved by the present invention easy to understand, the present invention will be further described below in conjunction with specific embodiments.
[0018] Such as figure 1 shown
[0019] A simple core-pulling method for blades with complex cavities based on UG modeling, including the following steps:
[0020] S1. Copy a 3D model of a complex cavity blade as the parent model 1 of core pulling, as a backup;
[0021] S2. Delete the area surface of the complex inner cavity of the original complex cavity blade model. In the area surface deletion, firstly select the area surface, the operation is to select any surface of the complex inner cavity as the seed surface 2, and all the surrounding inner cavity The surface is selected as the boundary surface 3. After confirmation, the entire inner cavity area surface is automatically identified, and the identified area surface is deleted through softwa...
PUM
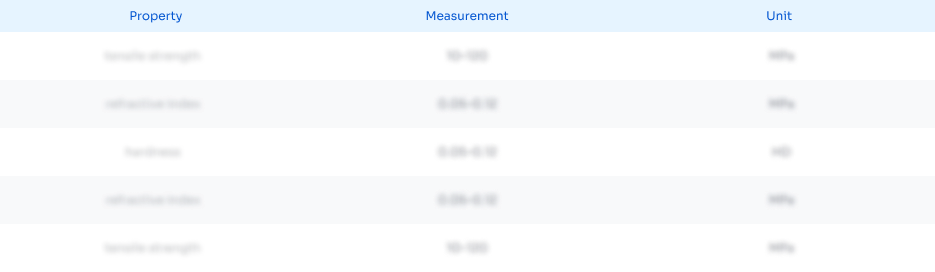
Abstract
Description
Claims
Application Information

- R&D
- Intellectual Property
- Life Sciences
- Materials
- Tech Scout
- Unparalleled Data Quality
- Higher Quality Content
- 60% Fewer Hallucinations
Browse by: Latest US Patents, China's latest patents, Technical Efficacy Thesaurus, Application Domain, Technology Topic, Popular Technical Reports.
© 2025 PatSnap. All rights reserved.Legal|Privacy policy|Modern Slavery Act Transparency Statement|Sitemap|About US| Contact US: help@patsnap.com